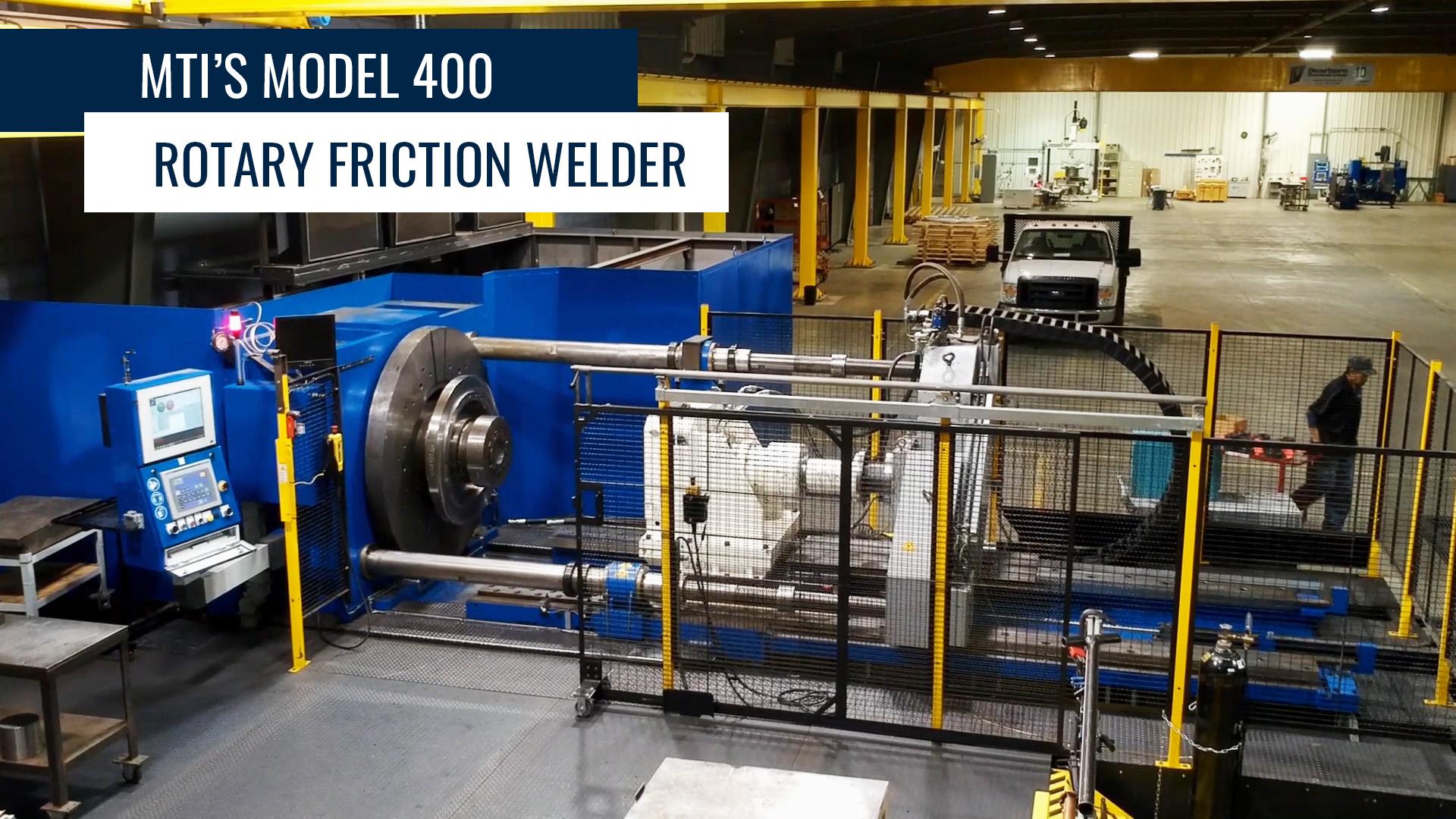
If you are looking for a machine with an impressive forge load capacity and limitless part length capabilities, then look no further than MTI’s Model 400 Contract Inertia Friction Welder. This one-of-a-kind machine is ready for your next project at our Manufacturing Services location in South Bend, Indiana.
There are so many ways you can benefit from this Rotary Friction Welding machine, such as allowing MTI to design and build custom tooling to guarantee your unique part will fit perfectly.
TOP REASONS TO CONSIDER MTI’S MODEL 400
- Largest inertia friction welder for contract friction welding
- A forge load capacity of 450 tons
- Limitless part length capabilities
- Ideal for aerospace and defense parts
- NADCAP and AS9100-certified
MACHINE SPECS
- Min Load: 69,300 lbs.
- Max Load: 923,640 lbs.
- Max Inertia: 118,095 lb-ft2
- Max RPM: 990 RPM
WHAT IS ROTARY FRICTION WELDING?
Let’s talk a little bit about Rotary Friction Welding and how it works.
Rotary Friction Welding is a solid-state process in which one part is rotated at a high speed and is pressed against another part that is held stationary. The resulting friction heats the parts, causing them to forge together.
UNIQUE ADVANTAGES OF ROTARY FRICTION WELDING
For your complex joining requirements, our Rotary Friction Welding solutions offer flexible options. MTI is a world leader in designing and manufacturing friction welders, and we are the only company offering all three types of rotary friction welding technologies – inertia, direct drive, and hybrid.
Here are some unique reasons why this technology could be great for you:
- Since dissimilar metals can be joined, a significant cost savings is possible
- Expensive forgings and castings can be replaced with less expensive forgings welded to bar stock, tubes, plates, etc.
- Significantly faster than conventional methods of welding
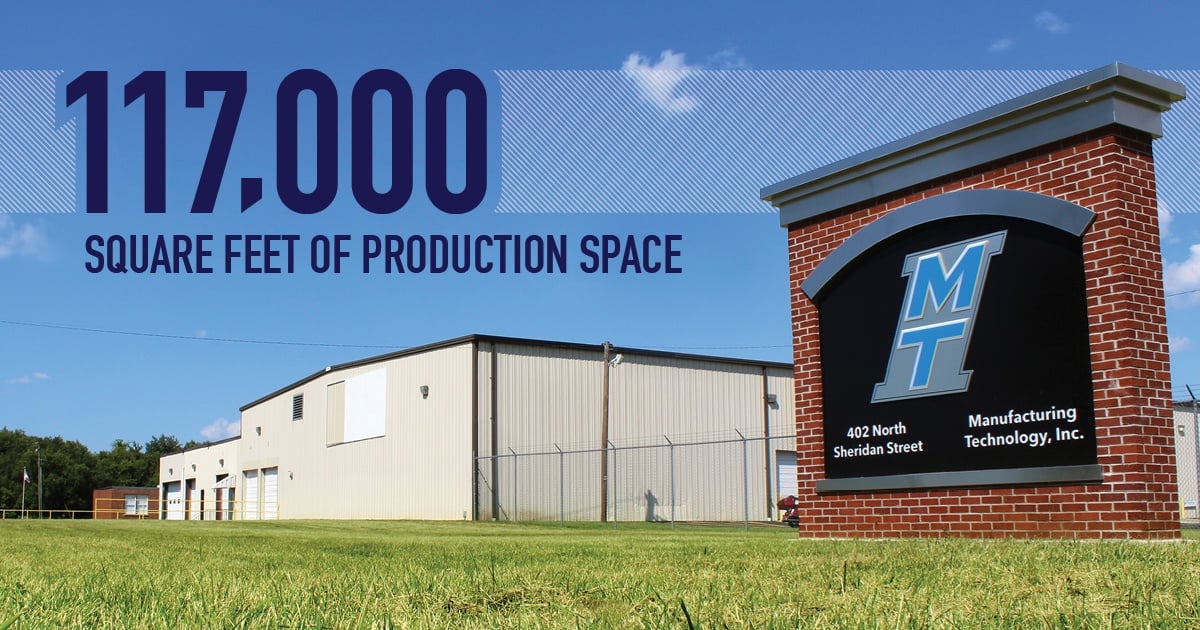
MANUFACTURING SERVICES FACILITY
Manufacturing Services is the root of MTI’s contract friction welding industry. This facility is roughly 117,000 square-feet and contains four loading docks, meaning we have the capacity to receive as well as ship large quantities of material.
At our contract friction welding location, we also have a full metallurgical lab. Our team can evaluate the weld quality during the weld development stage. From there, we will give you an elaborate weld report with our findings to help you determine your next step.
If you are a manufacturer that currently friction welds in-house, we can help provide a backup service to you in the event of scheduled down time, scheduled maintenance, or if you’re working with our machine build division building a new machine, we can provide a welding service for you during the build process as well.
BENEFITS OF MANUFACTURING SERVICES
- Weld Development – Optimizes the results that ensure the production parts are fit for purpose
- Prototyping – Early development benefits such as proving or disproving concepts and comparing performance
- Pre and Post-Weld Processing – Saving Time and Money; taking your project from concept to completion without needing to tap into outside resources
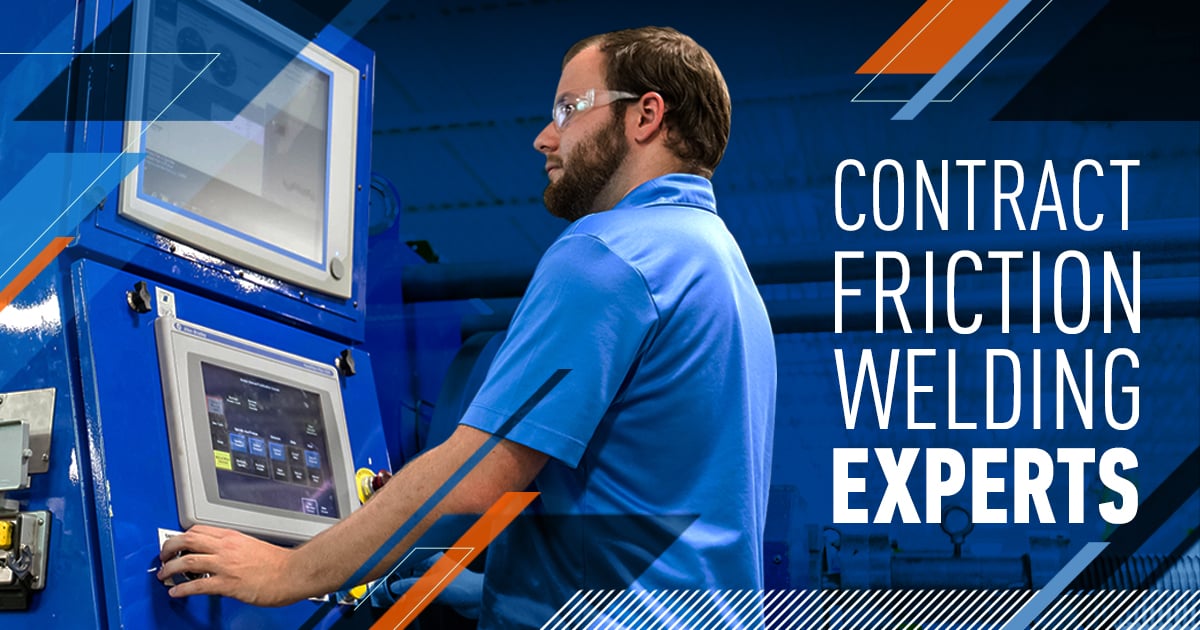
LET’S GET STARTED
Can your materials be friction welded? How does your part geometry play a role? Our team will tell you! Our weld development process is all about optimizing your friction welds.
Don’t have the volume to justify a new machine? We don’t just build friction welders – we operate them too! When you partner with MTI’s Contract Friction Welding Team, we will handle your project from start to finish on our state-of-the-art friction welding machines. Whether you need one part every year or one part every minute, we are here to help you reach your production goals!
Contact us today to learn more about the Model 400 Machine and explore how we can help improve your applications.