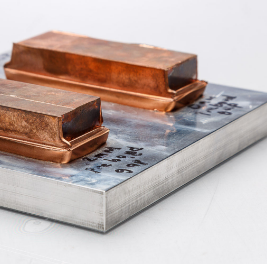
Contract Welding Services
MTI’s LF35-75 allows for the joining of the largest full-scale parts available. With over 20 blisk tooling sets, MTI can guide you through the end-to-end solution with part development through production.
The World’s Largest Manufacturer of Linear Machines
MTI not only designs and builds technically advanced LFW machines for the most critical of applications, we can also provide analytics services to ensure your machine is working at its best.
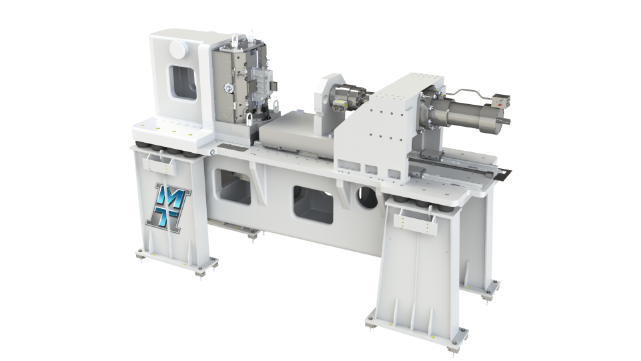
What is Linear Friction Welding?
The Aerospace Solution for 100% Butt Joint Weld
Linear Friction welding (LFW) is a specialized, solid-state joining process where one part oscillates in a linear motion against another while an axial thrust force is applied. The friction between the components heats the surfaces in contact creating a weld interface of plastic material that is forged together. LFW initially provided breakthrough solutions for the aerospace industry in the joining of “Blisks”, but has since been utilized in several other industries, providing new solutions for challenging applications.
Linear Friction Welding: Forging Industries Together
Linear Friction Welding (LFW) is a specialized, solid-state joining process in which one part moves in a linear motion at high speed and is pressed against another part held stationary. The resulting friction heats the parts, causing them to forge together. LFW initially provided breakthrough solutions for the aerospace industry in the joining of “blisks”, but has since been utilized in several other industries, providing new solutions for challenging applications.
Advantages & Benefits
An Emerging Solution for Unique Challenges
Linear Friction Welding provides a rapid, repeatable, and flexible process for manufacturers producing parts with various geometric shapes in many industrial markets. Here are some reasons why:
(Tailored/Close Contour Blanks)
Forged-quality Welds
Able to join a nearly limitless number of shapes and complex part geometries, Linear Friction Welding joints are of forged quality, with a 100-percent butt joint weld through the contact area. Linear Friction Welding can join dissimilar metals incompatible with conventional welding methods. This allows engineers to design bimetallic parts and near-net shape parts that use expensive materials only where needed.Near-Net Shape Manufacturing
(Tailored/Close Contour Blanks)
Using Linear Friction Welding to join near net shape parts with geometries designed to use expensive material only where needed provides a faster, much less expensive alternative to machining parts from solid blocks. The state-of-the-art machine has the largest tooling envelope of any linear friction welder in the world. It’s available now for full-sized part development in Detroit.
Full-scale Part Development
From blisks to bumpers, MTI’s LF35-75 is equipped to handle the largest parts in various industries. The state-of-the-art machine has the largest tooling envelope of any linear friction welder in the world. It’s available now for full-sized part development in Detroit.
Defect Free
MTI’s machine-controlled process eliminates human error, making the bond quality completely independent of an operator’s skill level. By reducing the number of defective parts fabricated, your investment of time and materials is put to its best use. Since there is no melting, solidification defects don’t occur in Linear Friction Welding, thus virtually eliminating gas porosity, segregation, or slag inclusions.Quick Weld Process
The Linear Friction Welding process is at least twice—and up to 100 times—as fast as other welding techniques. Multiple pieces can be bonded simultaneously, helping to reduce cycle time.
Able to join a nearly limitless number of shapes and complex part geometries, Linear Friction Welding joints are of forged quality, with a 100-percent butt joint weld through the contact area. Linear Friction Welding can join dissimilar metals incompatible with conventional welding methods. This allows engineers to design bimetallic parts and near-net shape parts that use expensive materials only where needed.
(Tailored/Close Contour Blanks)
Using Linear Friction Welding to join near net shape parts with geometries designed to use expensive material only where needed provides a faster, much less expensive alternative to machining parts from solid blocks. The state-of-the-art machine has the largest tooling envelope of any linear friction welder in the world. It’s available now for full-sized part development in Detroit.
From blisks to bumpers, MTI’s LF35-75 is equipped to handle the largest parts in various industries. The state-of-the-art machine has the largest tooling envelope of any linear friction welder in the world. It’s available now for full-sized part development in Detroit.
MTI’s machine-controlled process eliminates human error, making the bond quality completely independent of an operator’s skill level. By reducing the number of defective parts fabricated, your investment of time and materials is put to its best use. Since there is no melting, solidification defects don’t occur in Linear Friction Welding, thus virtually eliminating gas porosity, segregation, or slag inclusions.
The Linear Friction Welding process is at least twice—and up to 100 times—as fast as other welding techniques. Multiple pieces can be bonded simultaneously, helping to reduce cycle time.
Check Your Material Combination & Geometry
Can Your Application Be Friction Welded?
Compatible Welds
|
Not Seeing Your Combination Of Materials?
That doesn’t mean it can’t be done. Many of our material combinations are also proprietary. That’s why several of our customers use MTI’s in-house metallurgy lab, which will test your materials for strength and durability to see if friction welding is the right process for you.
Please note Weld strength is dependent on materials & geometry.
Joint Geometries
Linear Friction Welding can join a wide range of part geometries
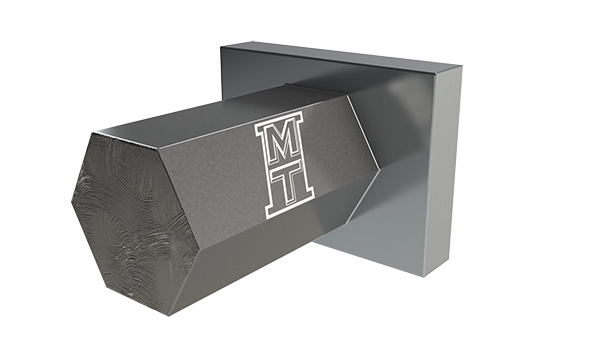
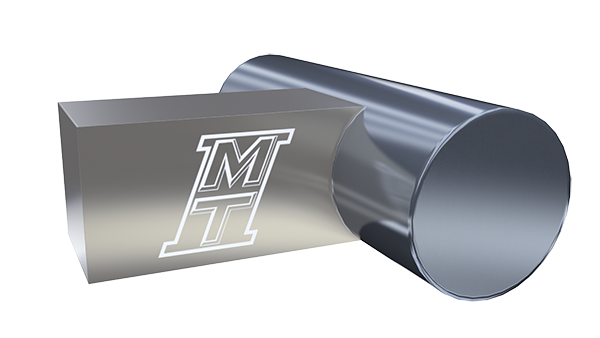
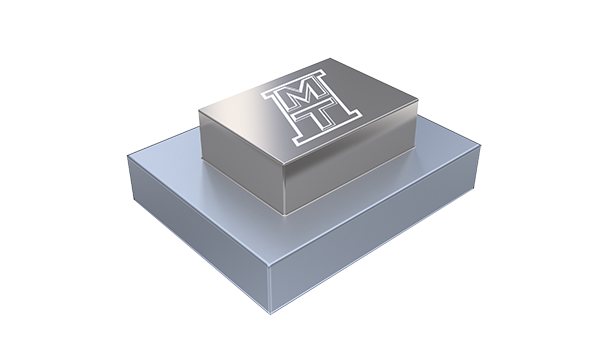
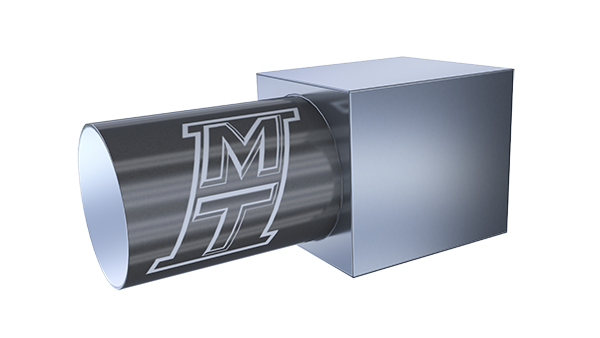
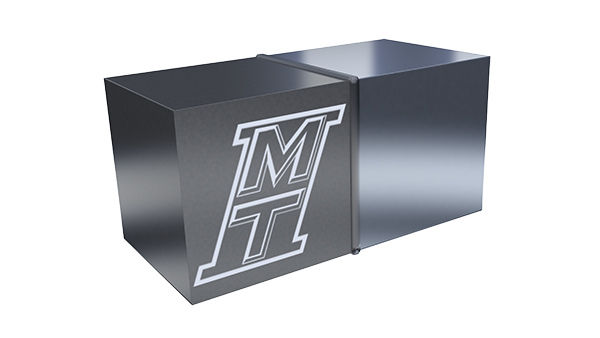
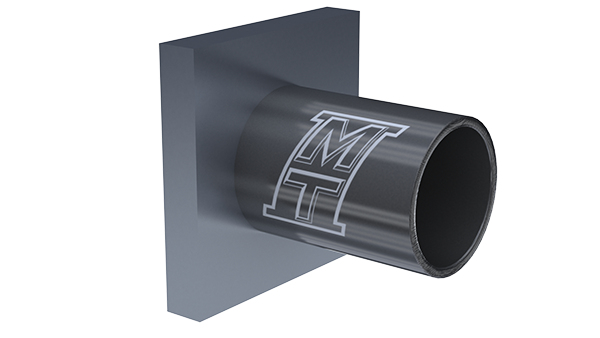
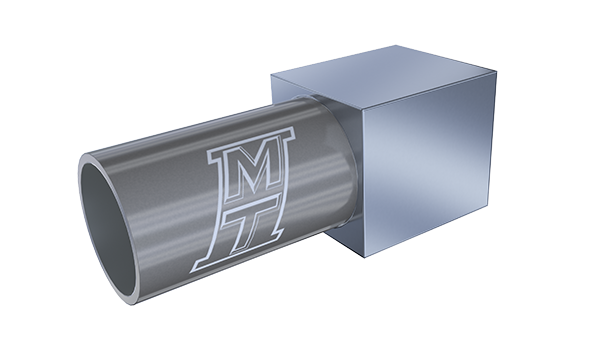
Let’s talk about the specifics of your project:
Linear Friction Weld
Low Force Friction Weld
Speed Up Cycle Times and Minimize the Flash
Low Force Opens Up More Innovations
We have a unique process that can accommodate smaller parts, thinner walls, unique geometries, and parts that can’t handle the process forces of traditional friction welding.
Linear Friction Welding Machines
For planes to go up and down, sometimes parts must go side to side. See why MTI is the leading manufacturer to have multiple Linear friction welders in operation around the globe.
Linear Friction Welding Machines
For planes to go up and down, sometimes parts must go side to side. See why MTI is the leading manufacturer to have multiple Linear friction welders in operation around the globe.
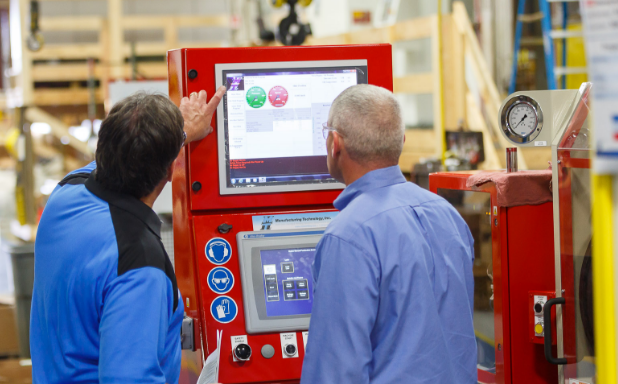
Maximize Production Performance
For mission critical applications, it’s essential to have confidence that your machine is performing optimally. MTI can provide analytics services to ensure your machine is functioning at its best.
Example Parts
We’d love to oscillate your mind with our Linear Friction Welded masterpieces, but alas, they’re so cutting-edge, they’re under lock and key. Just imagine the coolest parts you’ve never seen – that’s what we’re making!
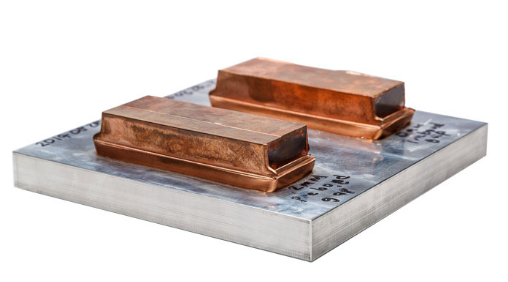
Application
Bimetallic Linear Development
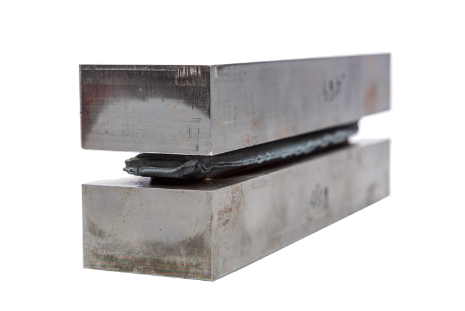
Application
Linear Development for Aerospace
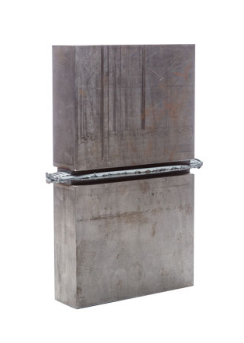
Application
Linear Development for Aerospace
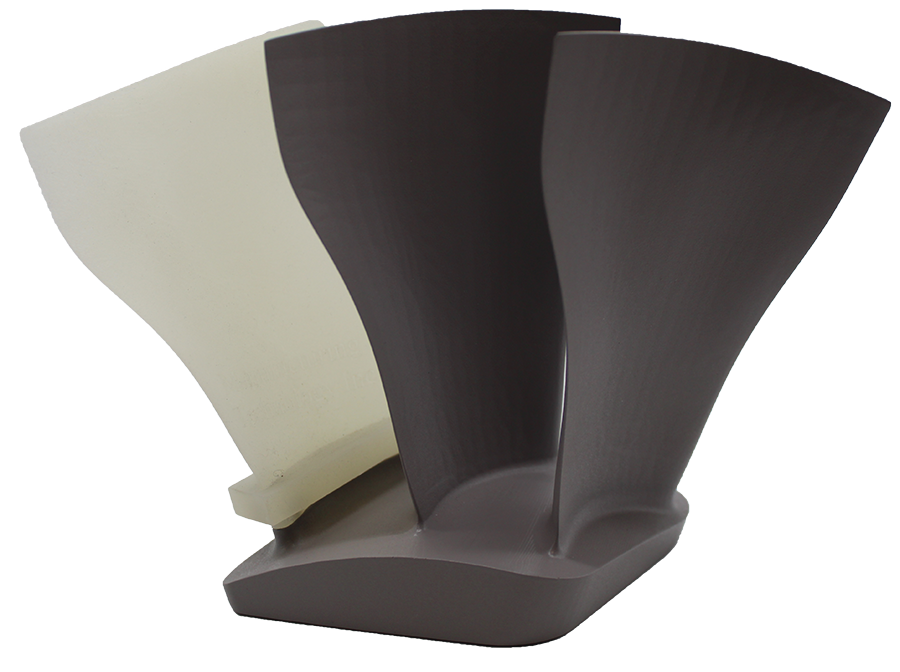
Application
3D Printed Blisk Model
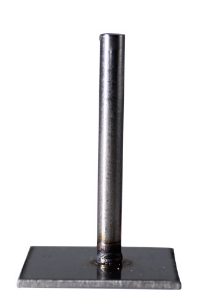
Application
Micro Linear Development
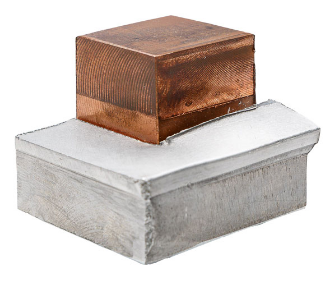
Application
Small-scale Bimetallic Linear Development
Contract Linear Friction Welding
Complete your project from design to production with us. Your global MTI contract friction welding team is here to help you design or build a part or a friction welder machine from start to finish in one location. At MTI, we have significantly contributed to the Aerospace and Automotive industries in collaboration with high-profile projects.
Contract Linear Friction Welding
Complete your project from design to production with us. Your global MTI contract friction welding team is here to help you design or build a part or a friction welder machine from start to finish in one location. At MTI, we have significantly contributed to the Aerospace and Automotive industries in collaboration with high-profile projects.
Learning Center
Featured Articles
Case Studies
Videos
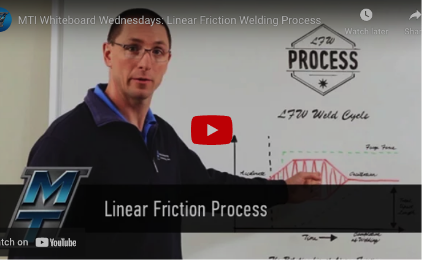
Whiteboard Wednesday
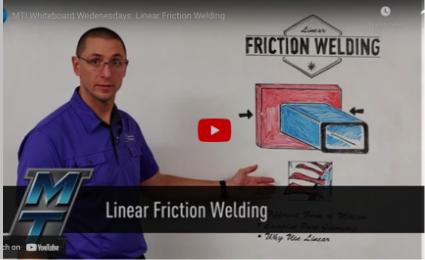
Whiteboard Wednesday
Get the information you need, before you need it — free and straight to your inbox from industry experts.