Rotary Friction Welding
Solid-State Revolution
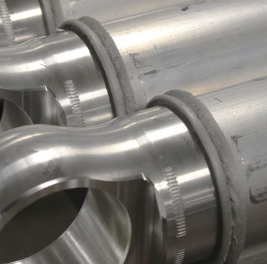
Contract Welding Services
We offer Rotary Friction Contract Welding services, specializing in bimetallic joining.
Rotary Machines
Learn about our Direct Drive, Inertia, and Hybrid Rotary friction welding machines.
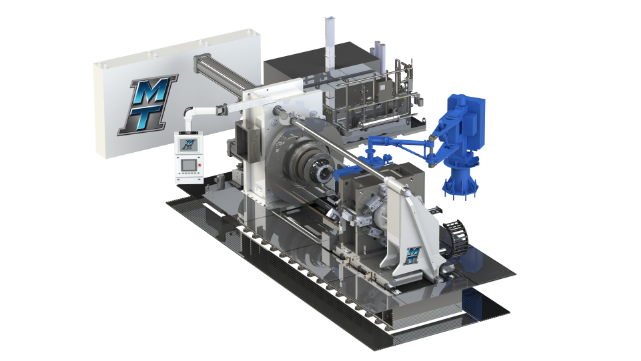
What is Rotary Friction Welding?
Less Joint Preparation, Faster Weld Cycles
Rotary Friction Welding is a solid-state process in which one part is rotated at high speed and is pressed against another part that is held stationary. The resulting friction heats the parts, causing them to forge together. This process is used across a number of industries such as automotive, aerospace, defense, consumer products and more.
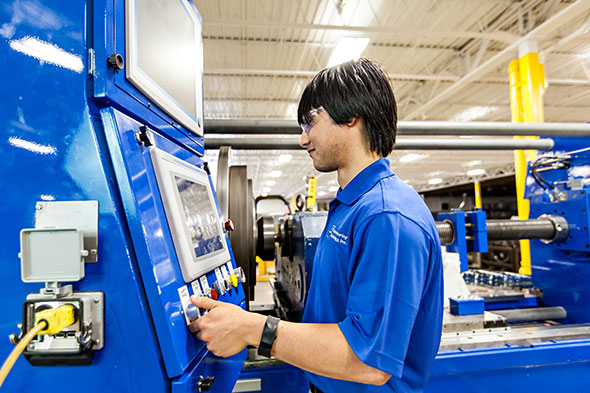
Low Force vs Traditional Friction Welding
Advantages & Benefits
Industry Trusted Joining Solution
Rotary friction welding offers high production efficiency, reduced operational costs, superior weld quality, and reliability, making it an ideal choice for industries demanding precision and durability.
Dissimilar Metals
One of the key differentiators between friction welding and other welding techniques is the ability to join dissimilar metals or two different materials that may be impossible to join by other techniques. Doing so is a cost effective way of getting the benefits from both materials.
Minimal Joint Preparation
Joint preparation isn’t as critical in the Rotary Friction Welding process – machined, saw-cut, and even sheared surfaces are weldable. Less joint preparation also lowers overall cycle time, allowing greater throughput in a production process.
Faster Weld Cycles
Rotary friction welding increases production efficiency by reducing the time required for each weld, leading to higher throughput in manufacturing processes. This enhancement lowers operational costs and ensures timely delivery of components, maintaining a competitive edge in industries where speed and reliability are crucial.
Machine-Controlled Process with Consistent Quality
Rotary friction welding delivers consistent part quality through its precise and repeatable process, where each weld is controlled by parameters to ensure uniformity. The integration of advanced automation further enhances this consistency, minimizing human error and maintaining high standards throughout production.
Green Process
When operating a rotary friction welding machine, no objectionable smoke, fumes or gases are exhausted into the atmosphere, making it one of the most environmentally friendly welding processes in use today. Plus, rotary friction welding does not require consumables, flux, filler materials or shielding gases.
One of the key differentiators between friction welding and other welding techniques is the ability to join dissimilar metals or two different materials that may be impossible to join by other techniques. Doing so is a cost effective way of getting the benefits from both materials.
Joint preparation isn’t as critical in the Rotary Friction Welding process – machined, saw-cut, and even sheared surfaces are weldable. Less joint preparation also lowers overall cycle time, allowing greater throughput in a production process.
Rotary friction welding increases production efficiency by reducing the time required for each weld, leading to higher throughput in manufacturing processes. This enhancement lowers operational costs and ensures timely delivery of components, maintaining a competitive edge in industries where speed and reliability are crucial.
Rotary friction welding delivers consistent part quality through its precise and repeatable process, where each weld is controlled by parameters to ensure uniformity. The integration of advanced automation further enhances this consistency, minimizing human error and maintaining high standards throughout production.
When operating a rotary friction welding machine, no objectionable smoke, fumes or gases are exhausted into the atmosphere, making it one of the most environmentally friendly welding processes in use today. Plus, rotary friction welding does not require consumables, flux, filler materials or shielding gases.
Check Your Material Combination & Geometry
Can Your Application Be Friction Welded?
Compatible Welds
|
Not Seeing Your Combination Of Materials?
That doesn’t mean it can’t be done. Many of our material combinations are also proprietary. That’s why several of our customers use MTI’s in-house metallurgy lab, which will test your materials for strength and durability to see if friction welding is the right process for you.
Please note Weld strength is dependent on materials & geometry.
Joint Geometries
Rotary Friction Welding can join a wide range of part geometries
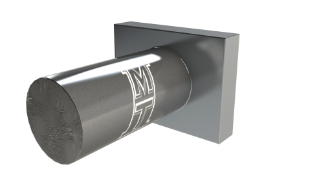
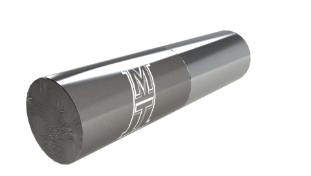
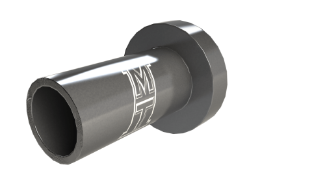
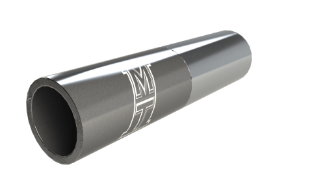

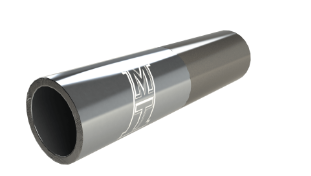
Let’s talk about the specifics of your project:
Low Force vs. Rotary Friction Weld
Smooth Flash. Low Upset.
Faster Cycle Times.
Ask Us About Low Force Friction Welding.
We have a unique process that can accommodate smaller parts, thinner walls, unique geometries, and parts that can’t handle the process forces of traditional friction welding.
Rotary Friction Welding Machines
Rotary Friction Welding Machines
MTI specializes in Rotary Friction welding in all forms – Direct Drive, Inertia, and Hybrid. Rotary Friction welding can accommodate various part geometries, being well-suited for applications across numerous industries. We manufacture a full line of machines including automated cells and specialty applications.
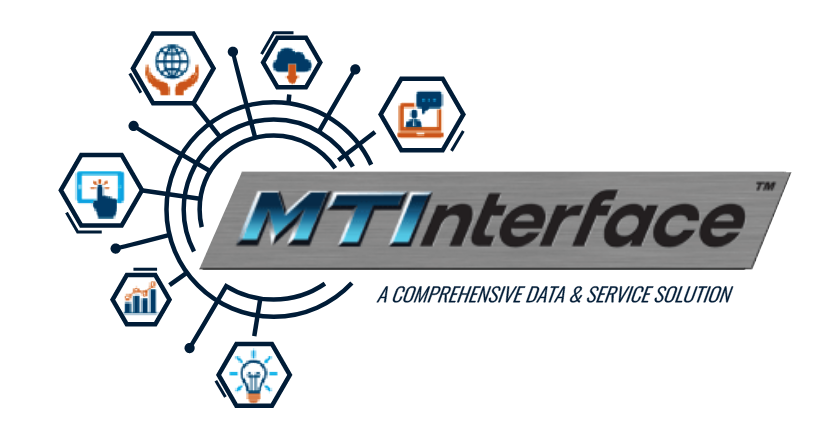
Industry 4.0
MTI now offers a comprehensive Industry 4.0 service solution for monitoring and improving machine performance!
Our new MTInterface Service Level Agreement (SLA) complements factory OEE requirements and provides actionable, machine-level data along with expert recommendations to ensure your friction welder consistently delivers the required performance – and value – to your organization.
Automation in Friction Welding
At MTI, our goal is to provide the next generation of autonomous integrated welding systems leveraging our world-class process knowledge and the latest in technology. With a focus on customized, low-risk configurations, we design and build a range of semi or fully automated welding machines tailored to requirements that deliver enhanced quality, productivity, and ROI.
Common Parts
Rotary friction welding can join a wide range of parts and geometries
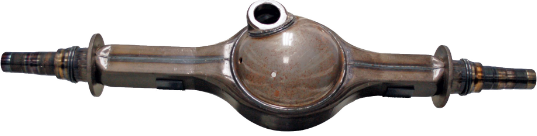
Application
Banjo Axle
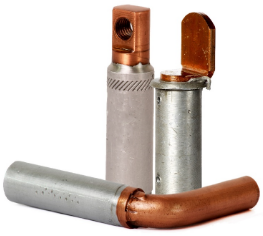
Application
Bimetallic electrical connectors
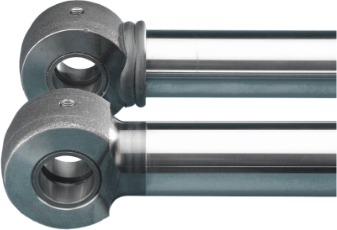
Application
Hydraulic Cylinder Rod
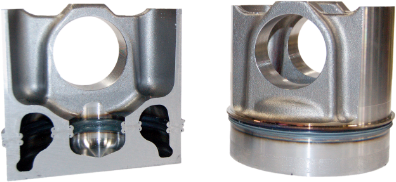
Application
Piston
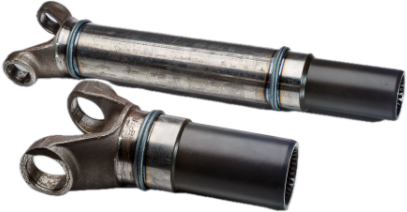
Application
Drive Shaft
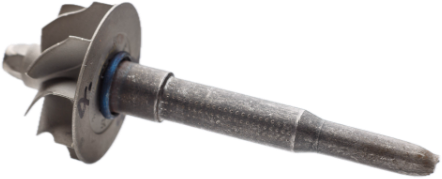
Application
Turbocharger
Contract Rotary Friction Welding
Contract Rotary Friction Welding
Learning Center
Case Studies
Videos
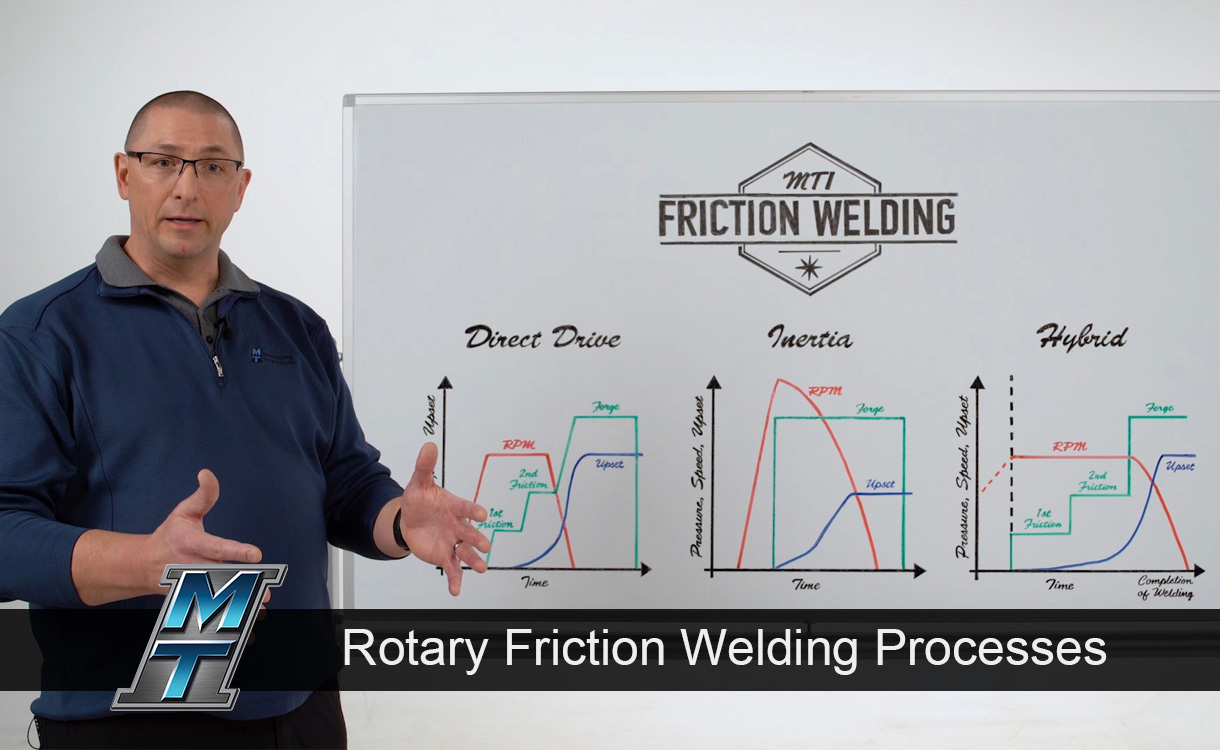
Whiteboard Wednesday
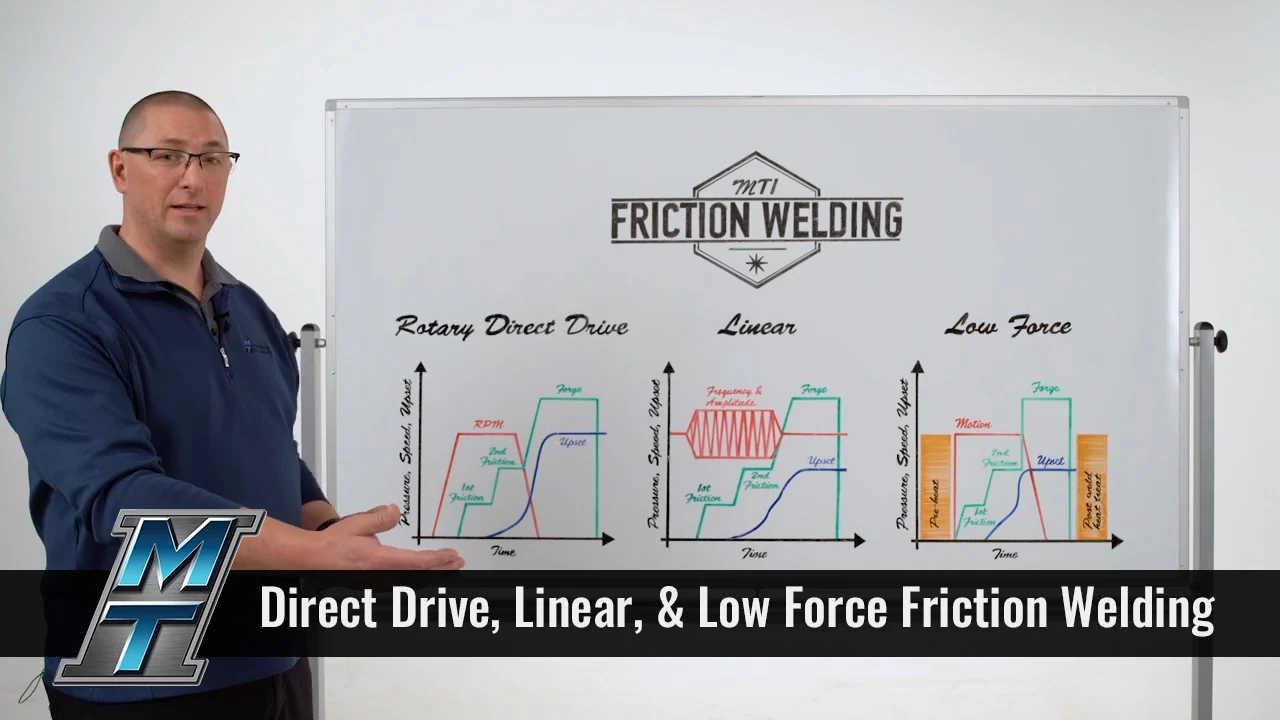
Whiteboard Wednesday
Get the information you need, before you need it — free and straight to your inbox from industry experts.
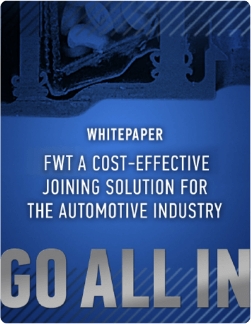
MTI White Papers
FWT: A cost-effective joining solution for the automotive industry
In the following pages, we will outline the benefits of friction welding, define the different types of friction welding, and describe the friction welding process. We’ll also mention current issues faced by the automotive industry. And finally, we’ll show how FWT is an effective tool to overcome these challenges and achieve manufacturing goals.