Design, Development, and Manufacturing of Spacecraft and Global Systems
Friction Welding for Astrospace Components
Meet the Welding Standards for the Astrospace Industry
MTI provides unparalleled expertise and state-of-the-art solutions for astronautic projects worldwide. We have partnered with NASA to help send astronauts to space, attaining a proud history of welding components for high-profile space missions.
MTI’s cutting-edge welding techniques effectively address the challenges faced in the astronautics sector, such as the need for super strong, reliable joints in extreme environments and the integration of dissimilar metals.
See how MTI has helped these manufacturers:
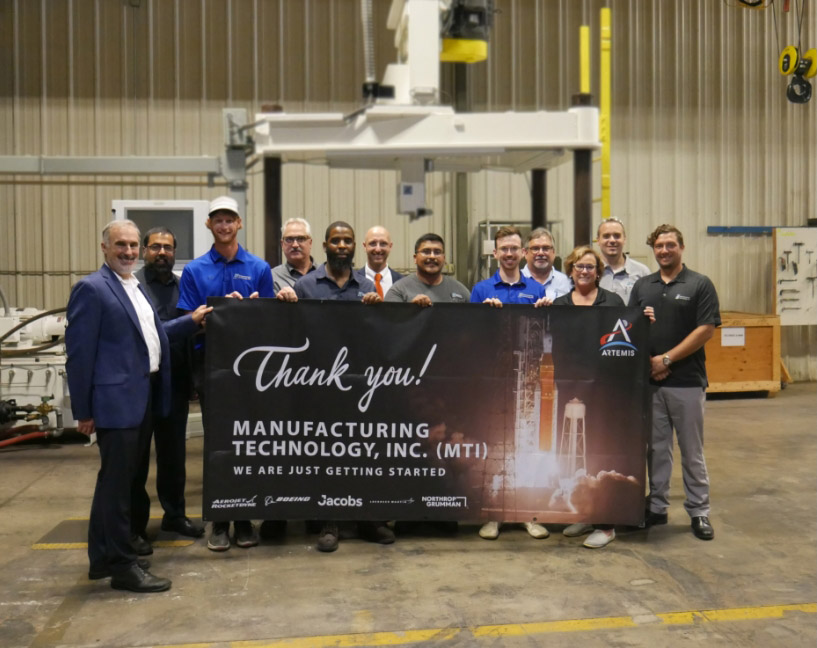
NASA and Aerojet Rocketdyne personnel with MTI’s Manufacturing Services team in front of the Vertical Rotary friction welder used to weld components for the RS-25 engines.
Advantages & Benefits
Propelling Astrospace Innovation to New Frontiers
MTI’s advanced friction welding technologies are pushing the boundaries of astrospace engineering. Our innovative solutions offer unparalleled capabilities in material joining, weight reduction, and component shaping, enabling the creation of spacecraft that are stronger, lighter, and more efficient for the challenges of space exploration.
(NNS/Close Contouring)
Bimetallic Joining
Friction Welding has the broadest capabilities of any welding method for joining dissimilar materials. In the astrospace industry, it is essential that welds are strong enough to withstand the harsh temperatures and environment of space travel. We worked with Ball Aerospace to develop a bimetallic solution for the TIRS-02 Cryocooler sensors by joining Copper to Titanium.
Lightweighting
The more a spacecraft weighs, the more fuel it needs to operate. Lightweighting can reduce the overall weight of the spacecraft, reducing costs and boosting fuel efficiency. Lightweighting is achieved by utilizing bimetallic combinations so that you only use the expensive material where it is absolutely critical.
Near-net Shape Components (NNS/Close Contouring)
Near-net shape friction welding helps the astrospace industry by producing components that are closer to their final (net) shape, significantly reducing the need for extensive post-weld machining and material removal. This leads to lower material costs and faster production times, improving overall efficiency. Additionally, the process results in stronger, more reliable joints, which are critical for the safety and performance of astrospace components.
R&D for Specialized Projects
For the astrospace industry, friction welding’s ability to work with advanced, unique, and challenging materials is a game-changer, enabling the development of high-performance, lightweight components essential for space missions. This is achieved through the solid-state nature of friction welding, which joins materials without melting them, preserving their properties and avoiding defects. The process supports cutting-edge research and development by allowing the reliable joining of dissimilar and exotic materials often required in astrospace applications. Consequently, it enhances the structural integrity and durability of spacecraft components, meeting the rigorous demands of space exploration.
Friction Welding has the broadest capabilities of any welding method for joining dissimilar materials. In the astrospace industry, it is essential that welds are strong enough to withstand the harsh temperatures and environment of space travel. We worked with Ball Aerospace to develop a bimetallic solution for the TIRS-02 Cryocooler sensors by joining Copper to Titanium.
The more a spacecraft weighs, the more fuel it needs to operate. Lightweighting can reduce the overall weight of the spacecraft, reducing costs and boosting fuel efficiency. Lightweighting is achieved by utilizing bimetallic combinations so that you only use the expensive material where it is absolutely critical.
Near-net shape friction welding helps the astrospace industry by producing components that are closer to their final (net) shape, significantly reducing the need for extensive post-weld machining and material removal. This leads to lower material costs and faster production times, improving overall efficiency. Additionally, the process results in stronger, more reliable joints, which are critical for the safety and performance of astrospace components.
For the astrospace industry, friction welding's ability to work with advanced, unique, and challenging materials is a game-changer, enabling the development of high-performance, lightweight components essential for space missions. This is achieved through the solid-state nature of friction welding, which joins materials without melting them, preserving their properties and avoiding defects. The process supports cutting-edge research and development by allowing the reliable joining of dissimilar and exotic materials often required in astrospace applications. Consequently, it enhances the structural integrity and durability of spacecraft components, meeting the rigorous demands of space exploration.
Our Commitment
Quality Consistency is the Root of Our Operations
MTI brings the highest possible degree of safety and quality, whether it’s a part we’re welding or a machine we’re building. We are equipped to produce parts for the most sensitive environments and exacting standards.
Friction Welding Machines for Astronautic Projects
Friction welding machines produce astronautic parts of consistent quality every time. With steady production and zero errors, they weld the most challenging metals to create spacecraft-worthy components.
Friction Welding Machines for Astronautic Projects
Friction welding machines produce astronautic parts of consistent quality every time. With steady production and zero errors, they weld the most challenging metals to create spacecraft-worthy components.
ROTARY FRICTION WELDING
EU and US Astrospace engine manufacturers use MTI-built rotary friction welding machines for rotor components, fan shafts, and more.
LOW FORCE FRICTION WELDING
MTI is the only company in the world to have developed and designed Low Force Friction Welding machines operating in production today.
LINEAR FRICTION WELDING
Need “near net shape” joining? Linear friction welding does it faster at a lesser cost than block machining.
FRICTION STIR WELDING
Friction Stir Welding’s solid-state joining process creates high-strength, defect-free welds, especially for aluminum alloys, which are widely used in Astrospace structures.
PLUG WELDING
Reduce the costs of maintenance repair for damaged holes in near-parent materials. MTI welcomes clients in need of Astrospace repair for fastener locations and more.
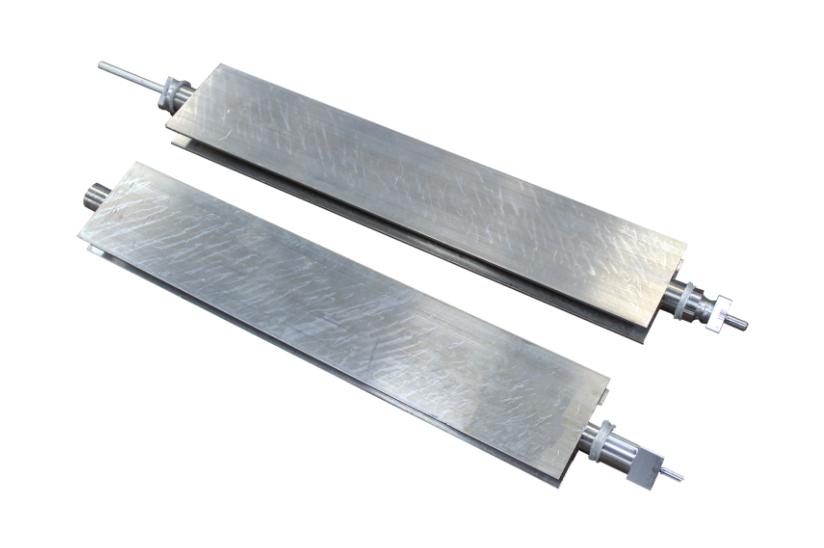
Explore Our Sample Parts
Browse our sample parts to discover applications, materials, and geometrical fittings for your next innovation.
Contract Manufacturing Services
We don’t just build machines, our Contract Manufacturing Services team operates them too. From part design to production, we have you covered.
Contract Manufacturing Services
We don’t just build machines, our Contract Manufacturing Services team operates them too. From part design to production, we have you covered.
Astrospace Friction Welding Machines for R&D
Put your materials and applications to the test with our line of in-house R&D machines.
Experiment with bimetallics and designer materials for your next project with MTI. We have machines in-house to allow you to explore possible innovations.
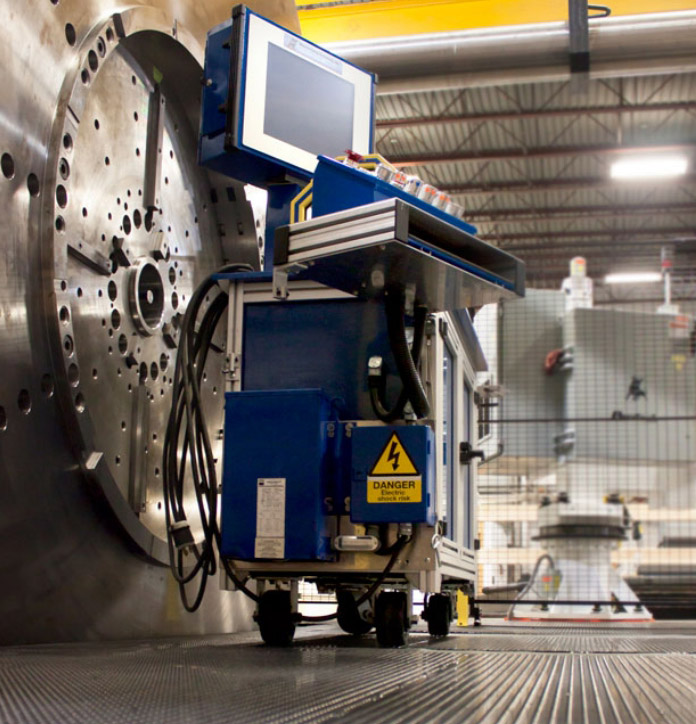
MTI’s “table-top” Model 40 Rotary friction welder used to join Astrospace components.
Learning Center
Featured Articles
Case Studies
Videos
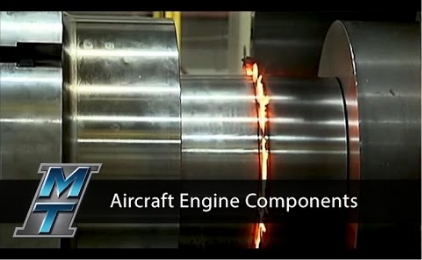
Astrospace Video
Get the information you need, before you need it — free and straight to your inbox from industry experts.