Welding Strength for the Energy Sector
Friction Welding for Oil & Gas Applications
Custom Engineered Approach to Oil Field Applications
The engineers and manufacturers of the Oil and Gas Industry face the pressure to make key components promptly and efficiently. At the same time, they need to create components for oil rigs that can withstand incredible stress.
For over 40 years, MTI has been the global manufacturer of friction welding machines that still operate today. Whether you want to improve a component, have one designed or manufactured for you, or have a friction welding machine made for your needs, we are here to make it happen.
Video courtesy of Zipp Industries GmbH & Co. KG. Video shows an MTI drill pipe machine being assembled.
Advantages & Benefits
Powering Efficiency and Safety in Oil and Gas Operations
MTI’s friction welding technologies are revolutionizing the oil and gas industry with unparalleled precision and durability. Our innovative solutions offer a perfect blend of efficiency, quality, and sustainability, enabling companies to enhance their operations while meeting the industry’s demanding safety and environmental standards.
Reduced Preparation
The reduced preparation of friction welding is crucial for the oil and gas industry as it significantly cuts down on production time and costs. Friction welding requires minimal surface cleaning and alignment for parts, making it ideal for quick, efficient repairs and assembly of pipelines and drilling equipment. Components do not have to be thoroughly cleaned before friction welding as the process actually acts as a surface cleaner for joining components.
Forged Quality
Friction welding is highly beneficial to the oil and gas industry because it produces exceptionally strong, defect-free joints that can withstand extreme pressures and temperatures. This is critical for the integrity and safety of pipelines and equipment in harsh environments. The process also reduces the need for additional materials or filler metals, which can enhance corrosion resistance and durability. As a result, it minimizes maintenance costs and extends the lifespan of critical infrastructure.
Machine-Controlled Process
Friction welding provides the oil and gas industry with precise, consistent, and repeatable welds, crucial for maintaining the high safety and performance standards required. The process automation minimizes human error and ensures uniform quality across large-scale production, which is essential for critical infrastructure like pipelines. It also increases production efficiency and reduces labor costs by streamlining the welding process.
Green Technology
Friction welding is beneficial for the oil and gas industry as it aligns with the growing emphasis on sustainable practices and reducing environmental impact. Friction welding generates less waste and emissions compared to traditional welding methods, which helps in minimizing your carbon footprint. Additionally, its lower energy consumption contributes to overall cost savings and promotes more sustainable operation. Friction welding’s environmental advantages support regulatory compliance and improve the industry’s reputation regarding environmental responsibility.
The reduced preparation of friction welding is crucial for the oil and gas industry as it significantly cuts down on production time and costs. Friction welding requires minimal surface cleaning and alignment for parts, making it ideal for quick, efficient repairs and assembly of pipelines and drilling equipment. Components do not have to be thoroughly cleaned before friction welding as the process actually acts as a surface cleaner for joining components.
Friction welding is highly beneficial to the oil and gas industry because it produces exceptionally strong, defect-free joints that can withstand extreme pressures and temperatures. This is critical for the integrity and safety of pipelines and equipment in harsh environments. The process also reduces the need for additional materials or filler metals, which can enhance corrosion resistance and durability. As a result, it minimizes maintenance costs and extends the lifespan of critical infrastructure.
Friction welding provides the oil and gas industry with precise, consistent, and repeatable welds, crucial for maintaining the high safety and performance standards required. The process automation minimizes human error and ensures uniform quality across large-scale production, which is essential for critical infrastructure like pipelines. It also increases production efficiency and reduces labor costs by streamlining the welding process.
Friction welding is beneficial for the oil and gas industry as it aligns with the growing emphasis on sustainable practices and reducing environmental impact. Friction welding generates less waste and emissions compared to traditional welding methods, which helps in minimizing your carbon footprint. Additionally, its lower energy consumption contributes to overall cost savings and promotes more sustainable operation. Friction welding’s environmental advantages support regulatory compliance and improve the industry's reputation regarding environmental responsibility.
Our Commitment
Innovating with Integrity, Delivering with Quality
MTI brings the highest possible degree of safety and quality, whether it’s a part we’re welding or a machine we’re building. We are equipped to produce parts for the most sensitive environments and exacting standards.
Friction Welding Machines for the Oil and Gas Industry
Machine-welded components are 100% solid-state bonded and are produced quickly and consistently, free of operator-made errors. This makes friction welding ideal for drill pipes, valves, and other drill stem components meant to withstand the high torque and rotary tension of directional drilling.
MTI offers the design and manufacture of friction welder machines, both semi and fully-automated, to meet the challenges of the oil and gas industry.
Friction Welding Machines for the Oil and Gas Industry
Machine-welded components are 100% solid-state bonded and are produced quickly and consistently, free of operator-made errors. This makes friction welding ideal for drill pipes, valves, and other drill stem components meant to withstand the high torque and rotary tension of directional drilling.
MTI offers the design and manufacture of friction welder machines, both semi and fully-automated, to meet the challenges of the oil and gas industry.
ROTARY FRICTION WELDING
MTI’s Rotary friction welding requires no prior joint preparation, saving time by not having to store pipes and other materials from the elements.
LOW FORCE FRICTION WELDING
Low Force friction welding can streamline production with a smoother flash on a wide range of parts.
LINEAR FRICTION WELDING
MTI’s Linear friction welding is proven to create stress-free superior joints, not through melting but through plasticization.
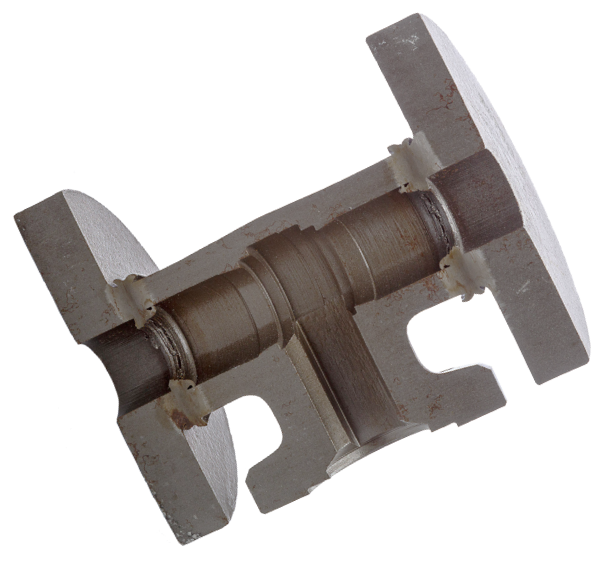
Explore Our Sample Parts
What you are wondering now has been done before. Explore our samples to find the ideal applications, materials, and geometric fittings for your next project in the oil and gas industry.
Contract Manufacturing Services
Our friction welding process equips you from start to finish. Whether you need to build friction welding machines or develop parts, we provide the in-house machines, lab, and knowledge necessary, including on-site service and training for operators and production assurance.
Contract Manufacturing Services
Our friction welding process equips you from start to finish. Whether you need to build friction welding machines or develop parts, we provide the in-house machines, lab, and knowledge necessary, including on-site service and training for operators and production assurance.
Oil and Gas Friction Welding Machines for R&D
Want to Make Oil and Gas Extraction Faster, Stronger, and Better?
Want to test your oil and gas project but don’t have the tools? MTI’s in-house friction welding machines are available for your R&D to optimize oil and gas extraction from rig site preparation to fracking. Test various materials and geometric fittings to ensure your project meets the demanding standards of your industry.
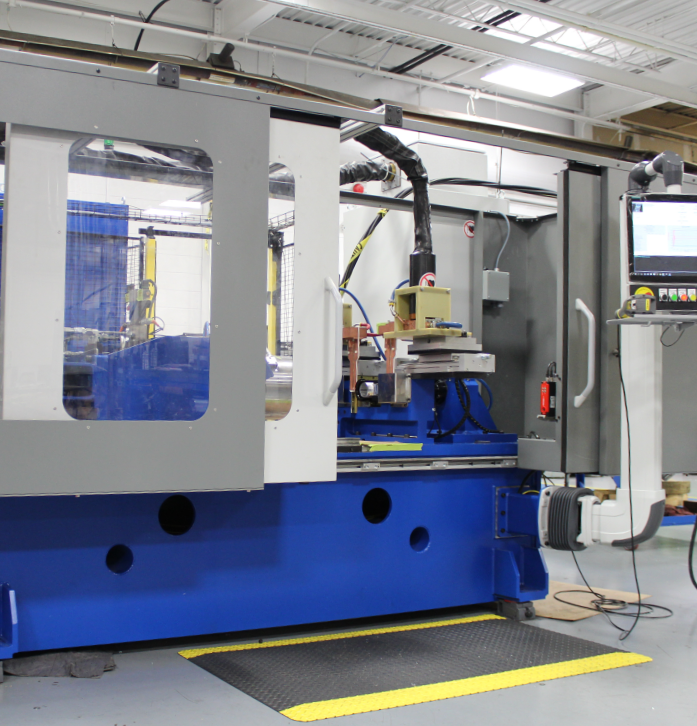
One of MTI’s Low Force Rotary lab machines.
Learning Center
Featured Articles
Case Studies
Videos
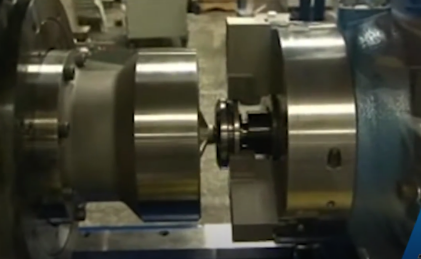
Oil & Gas Video
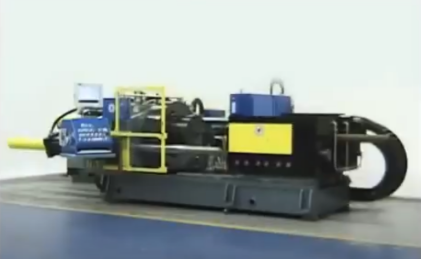
Oil & Gas Video
Get the information you need, before you need it — free and straight to your inbox from industry experts.