Welding Innovation for the Road Ahead
Friction Welding for Automotive Components
Automated Production and Repairs of Vehicular Components
MTI is the leading expert on friction welding technology worldwide. We collaborate with clients to design and manufacture friction welding machines that are still used today.
The automotive industry is experiencing a radical evolution with digitalization, electromobility, and lighter vehicles. Manufacturers must take advantage of friction welding to meet the demand for better vehicular quality. MTI assists in meeting this demand by advancing our friction welding processes.
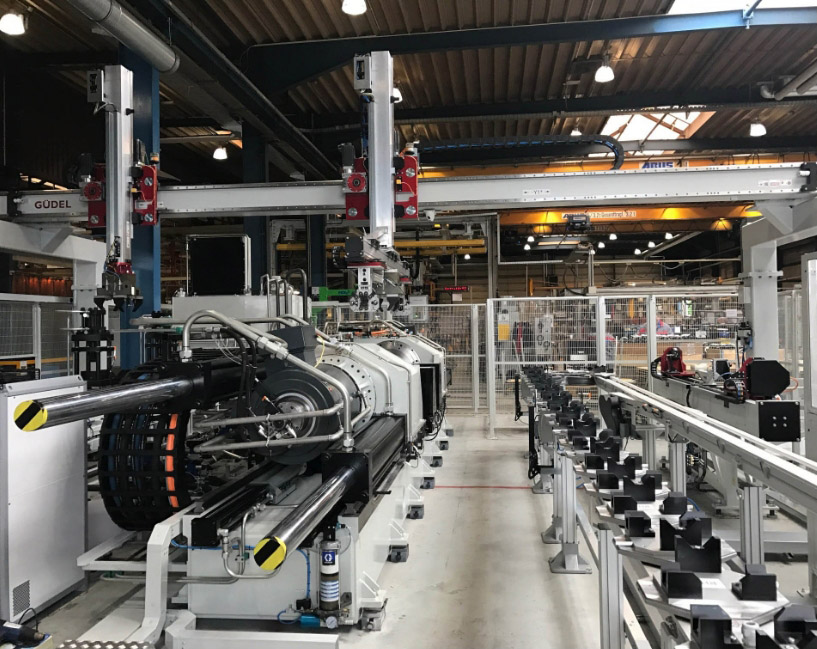
A recent MTI-built double ended friction welder for Axles incorporating full automation.
Advantages & Benefits
Driving Innovation in Automotive Manufacturing
MTI’s cutting-edge friction welding solutions are transforming the automotive industry. Our technologies offer a range of benefits that enhance vehicle performance, reduce costs, and support sustainable manufacturing practices.
Bimetallic Joining
Bimetallic friction welding benefits the automotive industry by enabling the joining of dissimilar metals, optimizing the use of lightweight and high-strength materials to enhance vehicle performance and fuel efficiency. This process provides strong, reliable joints without the need for additional fillers or adhesives, reducing manufacturing costs. It also improves corrosion resistance and extends component lifespan.
Lightweighting
Lightweighting with friction welding benefits the automotive industry by reducing vehicle weight through the use of bimetallics, which improves fuel efficiency and reduces emissions. The process creates strong, durable joints without adding excess material, supporting the use of lighter materials like aluminum. This enhances vehicle performance and handling.
Automated, Efficient Process
Friction welding is an automated process that removes the occurrence of operator error resulting in higher process efficiency. Friction welding uses predetermined calculations and measurements, all mechanically operated, that keep quality as consistent as the first weld. Additionally, friction welding cells can accommodate a fully automated work cell with the use of robots and gantry systems.
Green Technology
Friction welding is an eco-friendly technology that does not emit smoke, fumes, or gases. Friction welding does not require consumables such as flux or filler material, reducing your carbon footprint all the way down your supply chain as less material and energy is used.
Bimetallic friction welding benefits the automotive industry by enabling the joining of dissimilar metals, optimizing the use of lightweight and high-strength materials to enhance vehicle performance and fuel efficiency. This process provides strong, reliable joints without the need for additional fillers or adhesives, reducing manufacturing costs. It also improves corrosion resistance and extends component lifespan.
Lightweighting with friction welding benefits the automotive industry by reducing vehicle weight through the use of bimetallics, which improves fuel efficiency and reduces emissions. The process creates strong, durable joints without adding excess material, supporting the use of lighter materials like aluminum. This enhances vehicle performance and handling.
Friction welding is an automated process that removes the occurrence of operator error resulting in higher process efficiency. Friction welding uses predetermined calculations and measurements, all mechanically operated, that keep quality as consistent as the first weld. Additionally, friction welding cells can accommodate a fully automated work cell with the use of robots and gantry systems.
"Near-net shape” components can be created through Linear or Rotary Friction Welding, requiring minimal additional machining, saving costly time and materials. Airframe structures and blisks used in jet engine assemblies are two examples of parts created through near-net shape joining.
Our Commitment
Uncompromising Quality, Unmatched Excellence
MTI brings the highest possible degree of safety and quality, whether it’s a part we’re welding or a machine we’re building. We are equipped to produce parts for the most sensitive environments and exacting standards.
Friction Welding Machines for the Automotive Industry
Friction welding machines are proven to produce high-volume, consistent-quality welds for brake calipers, transmission gears, and more. No matter the size of your project, our friction welding experts will collaborate with you to provide specs to begin or help you build a customized friction welder solution.
Friction Welding Machines for the Automotive Industry
Friction welding machines are proven to produce high-volume, consistent-quality welds for brake calipers, transmission gears, and more. No matter the size of your project, our friction welding experts will collaborate with you to provide specs to begin or help you build a customized friction welder solution.
ROTARY FRICTION WELDING
Our legacy in rotary friction welding, Direct Drive, is the automated solution for parts such as piston rods, axles, and more.
LOW FORCE FRICTION WELDING
Do you need parts joined with minimal flash formation? MTI is the sole company that manufactures Low Force friction welding machines that are still operating in production today.
FRICTION STIR WELDING
Friction Stir Welding is vital for sensitive automotive parts to ensure driving safety. In MTI, we use this type of welding to seal high-strength battery trays and heat exchangers.
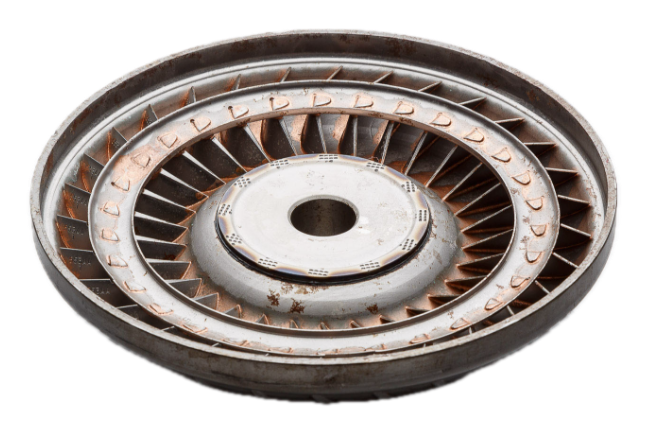
Explore Our Sample Parts
Explore our sample parts to find the perfect applications, materials, and geometric fittings for your next project.
Contract Manufacturing Services
If you have a project in mind, we’re here to optimize your friction welds. We offer everything from an in-house metallurgical lab to a machine shop to help you customize small parts to heavy machinery.
Contract Manufacturing Services
If you have a project in mind, we’re here to optimize your friction welds. We offer everything from an in-house metallurgical lab to a machine shop to help you customize small parts to heavy machinery.
Automotive Friction Welding Machines for R&D
Want to test your new project but don’t have the tools?
MTI has in-house friction welding machines available for your research and development needs. Test materials, parts, and geometric fittings.
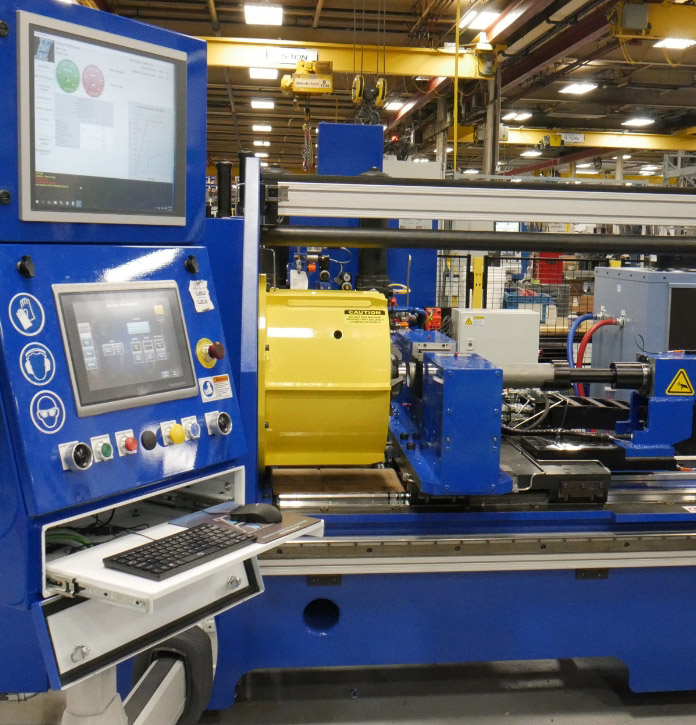
MTI Model 40T Rotary friction welder housed at our Manufacturing Services facility.
Learning Center
Featured Articles
Case Studies
Videos
Get the information you need, before you need it — free and straight to your inbox from industry experts.