Your Contract Friction Welding Partner
From Concept Through Completion
❭ North America
❭ North America
❭ Europe
❭ Europe
❭ Asia
❭ Asia
World Leader in Friction
Welding Technology
World Leader in Friction
Welding Technology
Feasibility Studies & Prototypes
From Feasibility to Full
Production We've Got
You Covered
Harness the versatility of friction welding with our expert Manufacturing Services team. We bring innovative approaches and timely results to your advanced research and part production needs. Whether you’re looking for one part per year or one per minute, we’re committed to helping you achieve your production goals.
Contract Friction Welding Services
We Can Help You Reach Your Part Production Goals
Cost Savings
You can save time and money, while also reducing the number of steps to reach your production goal, by taking advantage of MTI’s design experience in the prototype stage. We know what works and what doesn’t, based on our years of development experience and large portfolio of successfully welded production parts – parts that started as prototypes.
Material Evaluations
Our on-staff experts have decades of experience. This allows us to offer a full-range of detailed metallurgical testing and evaluations to confirm physical properties of the part and the weld zone.
Custom Design Capabilities
Explore new designs and applications without workflow disruptions in your manufacturing facility. We recommend, design, and prototype unique and innovative solutions to the product development and improvement process that can expose additional savings and technical value to new and existing designs.
Production Evaluation
Our metallurgy capabilities extend to after your part is welded. Using our tensile tester and a series of other strength tests, we can ensure the weld meets your requirements.
You can save time and money, while also reducing the number of steps to reach your production goal, by taking advantage of MTI’s design experience in the prototype stage. We know what works and what doesn’t, based on our years of development experience and large portfolio of successfully welded production parts – parts that started as prototypes.
MTI’s Contract Manufacturing Services group has decades of experience and can evaluate your material before it’s welded to ensure the weld will be of optimal strength. MTI’s Process Engineers also work to ensure the joint strength meets your requirements.
Our customers’ parts are all different shapes and sizes – but so is our tooling! If your part doesn’t fit in existing MTI tooling, we’ll custom design new tooling for you.
Our metallurgy capabilities extend to after your part is welded. Using our tensile tester and a series of other strength tests, we can ensure the weld meets your requirements.
Comprehensive Weld Development
Can your materials be friction welded? How does your part geometry play a role? Our friction welding experts will tell you! Our weld development process is all about optimizing your friction welds. Once we evaluate your materials and produce sample parts, we will provide you with the specs to either begin joining or to help build a friction welder that’s right for your project.
Comprehensive Weld Development
Can your materials be friction welded? How does your part geometry play a role? Our friction welding experts will tell you! Our weld development process is all about optimizing your friction welds. Once we evaluate your materials and produce sample parts, we will provide you with the specs to either begin joining or to help build a friction welder that’s right for your project.
Weld Development 2.0
In this new package, MTI tests the feasibility of your application with traditional friction welding as usual, but we also perform Low Force friction welding test welds so you can compare the benefits of the new technology directly with the traditional friction welding processes.
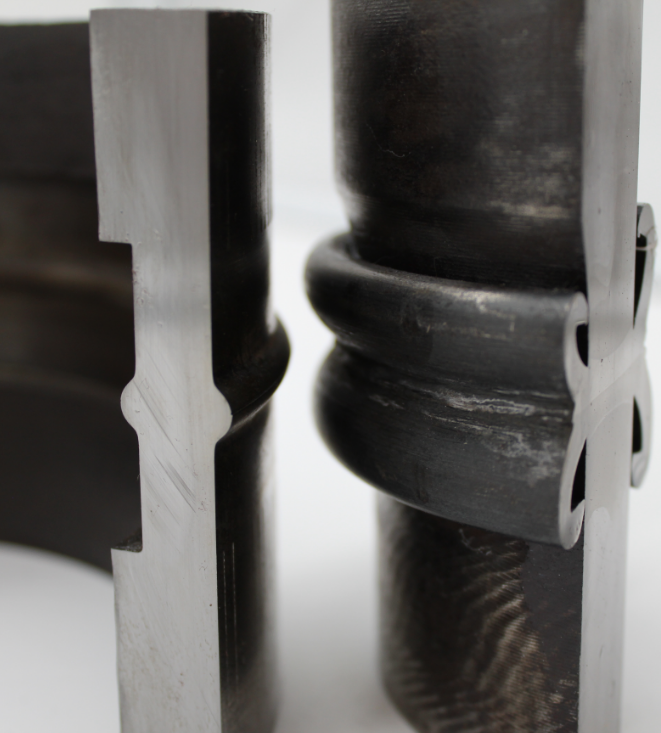
Low Force versus traditional Friction Welding
Friction Welding Concept & Prototype Examples
Manifold Tubing
- Creates narrow heat-affected zone
- 100% bond of contact area
- Resulting joints are of forged quality
- Stronger than parent material
- No weld splatter is created
Finished Clutch Drum
- Dissimilar Materials - 4118 carburized and hardened gear to 1045 Drum
- Greatly increase design flexibility
- Choose appropriate materials and material size for each area of part
- Assembly is complete after welding
Bimetallic Exhaust Valves
- Dissimilar Materials - High temperature resistant valve to high wear resistant alloy stem
- Lower costs as bimetallic application
Stabilizer Bars
- Dissimilar Materials – 4130 Steel tubing with 1018-1020 solid ends welded on each end
- Lightweight, but durable
- Save weight while maintaining torque and fatigue characteristics
Oil Field Valve Body
- Various end fittings inertia welded to standard valve bodies
- Reduces inventory of many different valve body castings
- Replaced single casting
Track Roller Bushings
- Steel backed, bronze laminate thrust washer to steel sleeve
- Reduce raw material and machining costs
- Replaced solid bronze casting
- Annual cost savings after taxes is nearly twice the cost of the purchase price of the machinery
Lift Screws
- Roll threaded stock, saw cut to length and welded to screw machined ends
- Reduce raw material costs
- Reduction in machining costs
Actuator for Reciprocating Saws
- Mild steel injection molded head (to size)
- Mild steel spindle tube to reduce weight - for directional changes (reciprocating)
- Less cost than a finished product made from a forging or casting
Pre & Post-Weld Process
Our friction welding process starts well before your parts touch our friction welders and long after they come off the machines. From our in-house metallurgical lab to a machine shop equipped to develop custom tooling, we can take your project from concept to completion without needing to tap into outside resources. This efficiency saves time and shipping costs.
Friction Welding Technologies
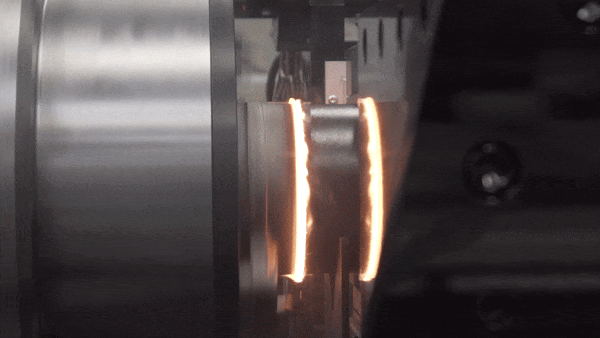
ROTARY FRICTION WELDING
Rotary friction welding (RFW) is a solid-state process where one component is rotated at high speed and pressed against a stationary part. RFW is a widely used technique across several industries, offering unparalleled advantages. Our contract Manufacturing Services facilities have more than 15 combined RFW machines including the world’s largest Inertia contract friction welder.
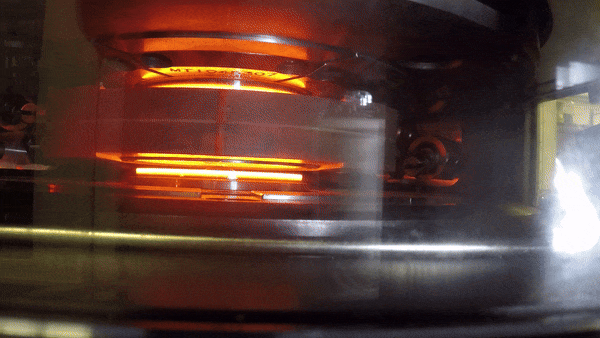
Low Force FRICTION WELDING
Low Force friction welding is our newest solid-state process and utilizes an external heat source to weld the components, reducing the forces required compared to traditional friction welding. Low Force friction welding introduces many benefits across applications including less flash formation, faster weld cycles, and controlled cooling rates. Our contract Manufacturing Services group has 5 Low Force laboratory R&D machines available for your development and production work!
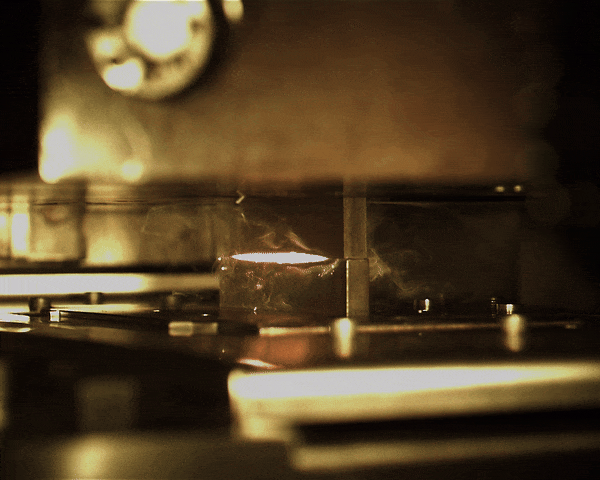
Linear Friction Welding
Linear friction welding (LFW) is a solid-state process that uses linear motion to join one component to a stationary component. LFW has the unique ability to join non-symmetrical and complex components, making it an ideal choice within the Aerospace industry. Our contract Manufacturing Services group is home to the largest Linear friction welding machine in the world, capable of producing full-size parts for any application.

Friction Stir Welding
Friction Stir welding (FSW) is a solid-state process that creates friction by rotating a pin tool into the parts to be joined, stirring the materials together and creating a watertight seal. FSW is becoming increasingly popular following today’s electrification of cars, trains, and planes. Our contract Manufacturing Services group has 4 Friction Stir welders that are ready to handle your R&D and production work.
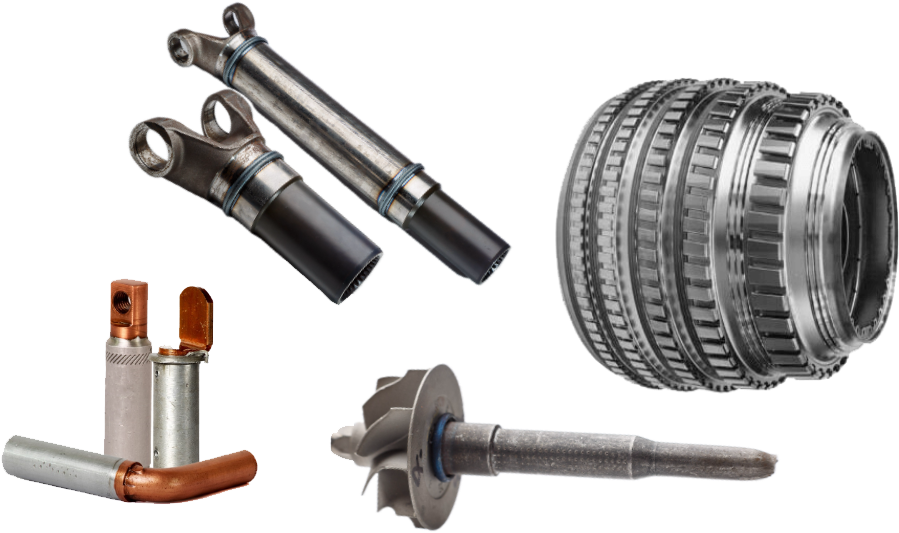
Explore Our Sample Parts
View our sample friction welded parts catalog to uncover applications that might be right for your next project.
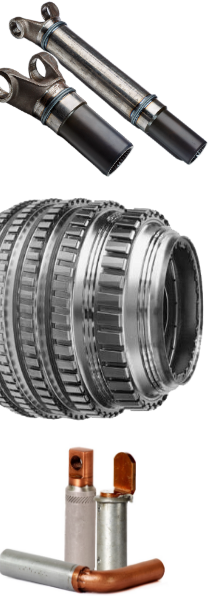
Explore Our Sample Parts
View our sample friction welded parts catalog to uncover applications that might be right for your next project.
Bi-Metallic Joining
From Copper and Aluminum to Steel and Inconel, friction welding allows for the joining of dissimilar metals – and there’s no better place to try out your combination than with our global Contract Friction Welding teams! Allow us to test your materials for strength and durability, and then learn how your combination could benefit your overall process!
Cut Costs, Not Quality
You can save time and money, while also reducing the number of steps to reach your production goal, by taking advantage of MTI’s design experience in the prototype stage. We know what works and what doesn’t, based on our years of development experience and large portfolio of successfully welded production parts – parts that started as prototypes.
Trim Weight Where It Matters
Bimetallic friction welding can help achieve your lightweighting goals by only using heavier materials on your part where it’s absolutely necessary. This ensures your product’s quality and integrity are not compromised.
Unleash Your Part’s Full Potential
Not all welding methods are created equal. Friction welding has the broadest capabilities for joining dissimilar metals which can strengthen your part’s design.
Reduced Equipment Wear
MTI helped extend the service life of equipment for a Canadian oil sands producer, thanks to linear friction welding and the combination of tungsten and steel and intermediate materials.Bi-Metallic With Low Flash & Low Force
The possibilities of joining dissimilar metals can be even broader with our newest solid-state joining technology!
Bi-Metallic Joining
From Copper and Aluminum to Steel and Inconel, friction welding allows for the joining of dissimilar metals – and there’s no better place to try out your combination than with our Contract Friction Welding teams in our US or UK locations! Allow us to test your materials for strength and durability, and then learn how your combination could benefit your overall process!
You can save time and money, while also reducing the number of steps to reach your production goal, by taking advantage of MTI’s design experience in the prototype stage. We know what works and what doesn’t, based on our years of development experience and large portfolio of successfully welded production parts – parts that started as prototypes.
Bimetallic friction welding can help achieve your lightweighting goals by only using heavier materials on your part where it’s absolutely necessary. This ensures your product's quality and integrity are not compromised.
Check Your Material Combination & Geometry
Can Your Application Be Friction Welded?
Compatible Welds
|
Not Seeing Your Combination Of Materials?
That doesn’t mean it can’t be done. Many of our material combinations are also proprietary. That’s why several of our customers use MTI’s in-house metallurgy lab, which will test your materials for strength and durability to see if friction welding is the right process for you.
Please note Weld strength is dependent on materials & geometry.
Joint Geometries
Friction Welding can join a wide range of part geometries
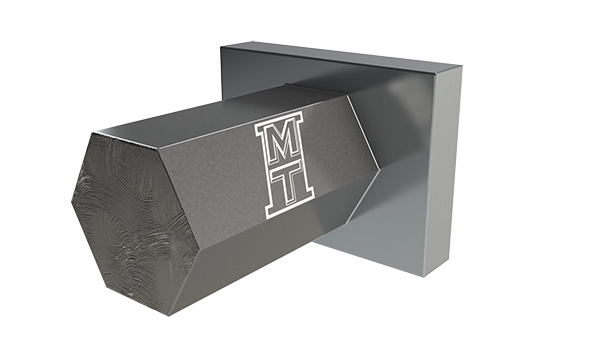
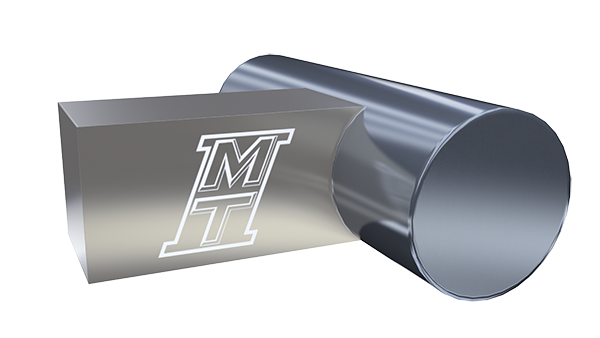
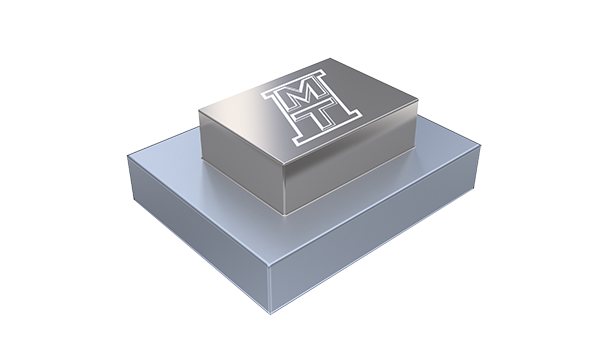
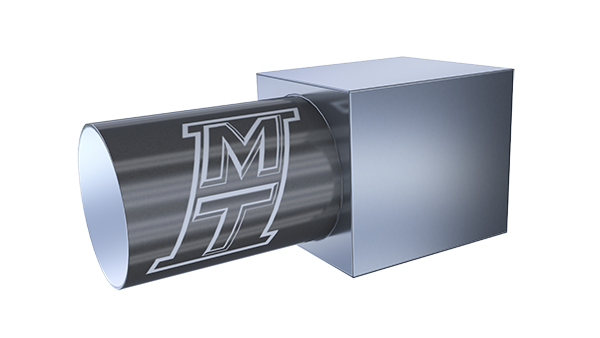
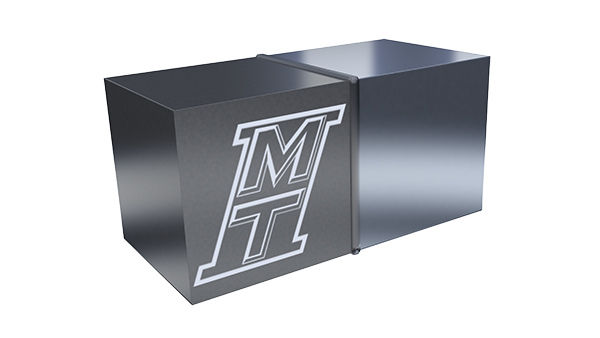
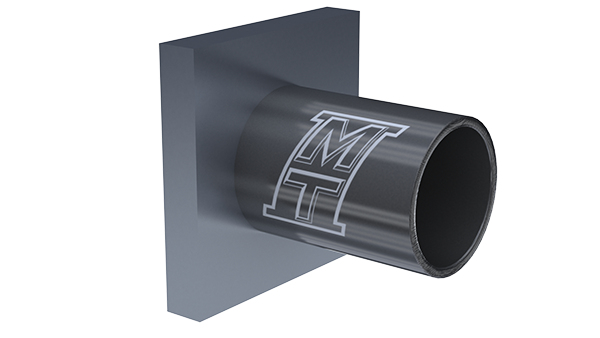
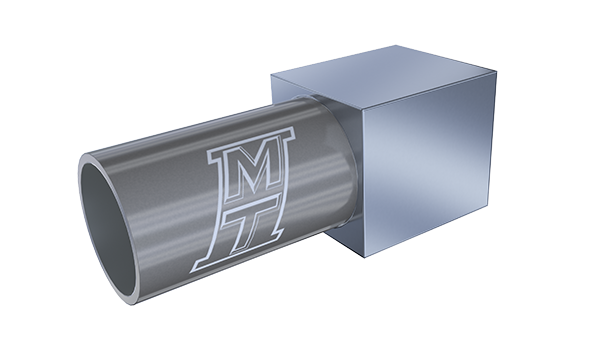
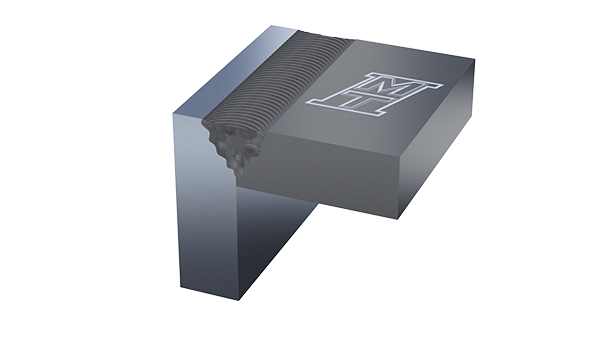
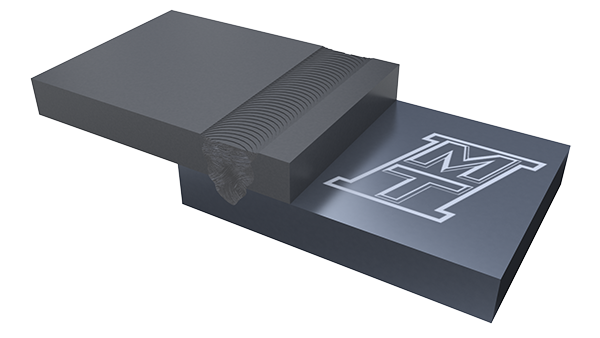
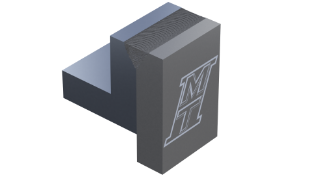
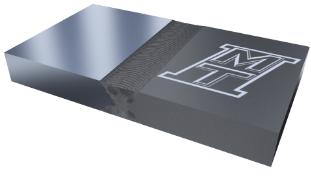
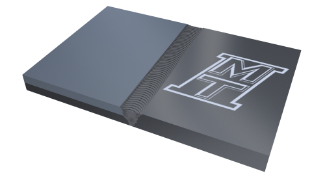
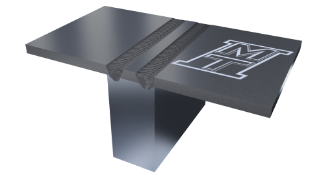
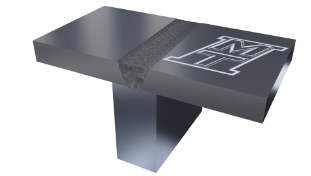
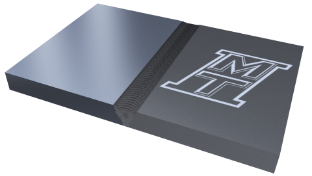
Let’s talk about the specifics of your project:
Production Assurance Program
Our contract friction welding group isn’t just for customers who don’t have their own friction welders. Our Production Assurance Program helps bridge the gap if your MTI-built friction welder is undergoing routine maintenance or if you experience higher-than-normal part volumes. Let us keep your tooling warm and handle your overflow on our machines, without any breaks in your production process.
Learning Center
Featured Articles
Case Studies
Videos
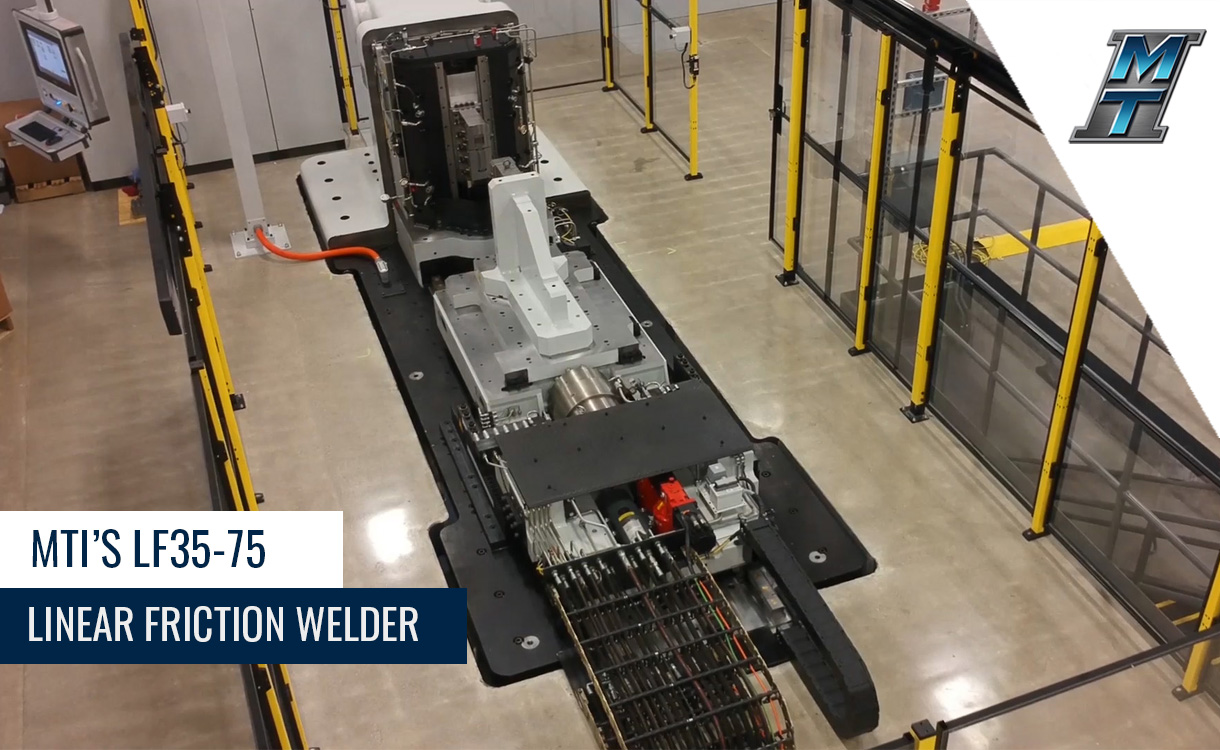
Aerospace Video
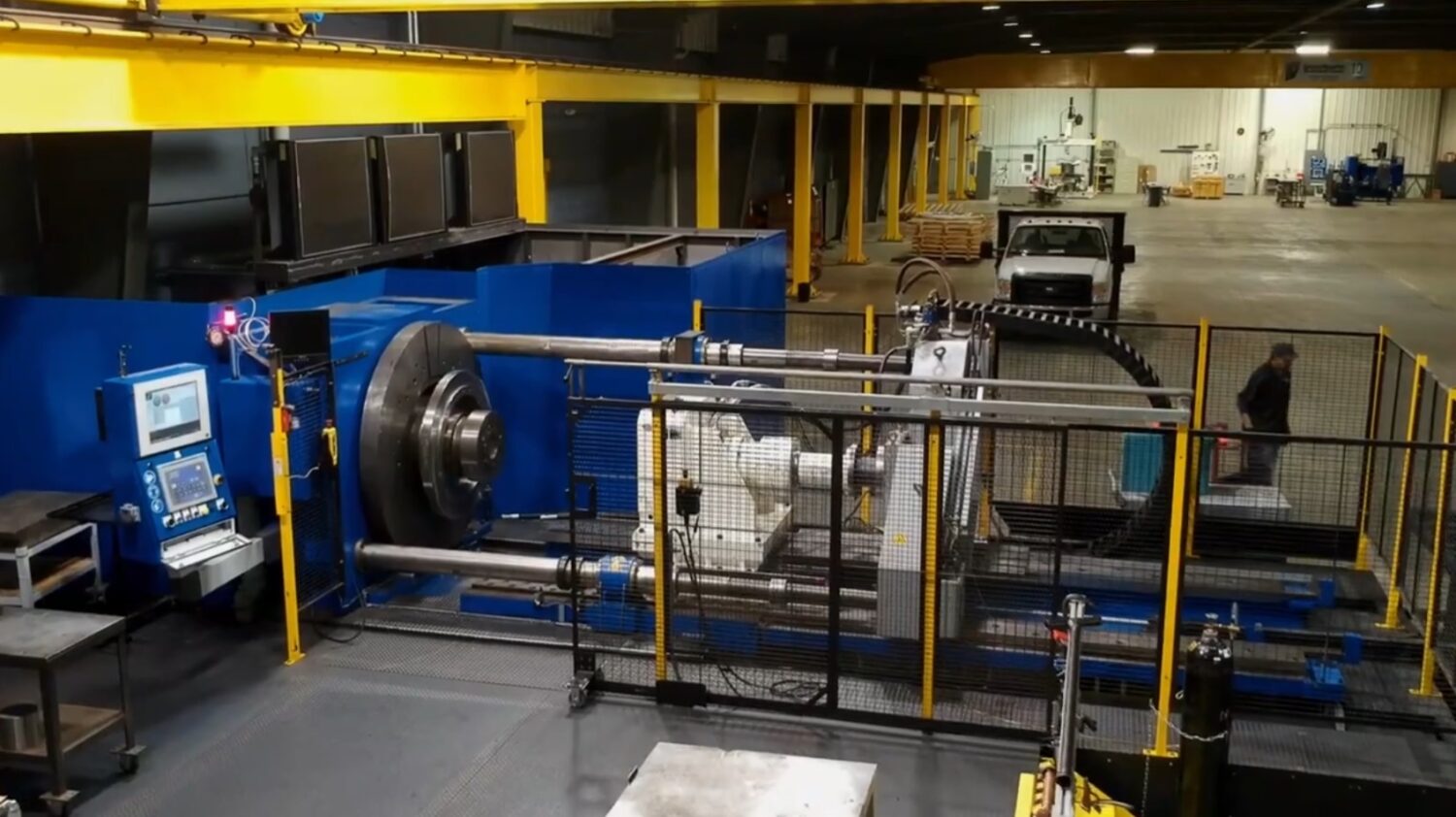
Aerospace Video
Get the information you need, before you need it — free and straight to your inbox from industry experts.