What is Friction Welding?
A Guide to Friction Welding Technologies
Friction welding is a solid-state joining technique that welds a joint between two components through mechanical heat friction. This welding technology has been a trusted and effective joining process for decades, evolving into various specialized techniques such as Rotary, Linear, Friction Stir, and Low Force friction welding. As the only manufacturer that offers all of these friction welding processes, MTI is uniquely positioned to recommend and supply the best technology for your application. Our decades of experience in the industry provide us with a deep understanding of the nuances and advantages of each method, ensuring that we can provide a tailored solution to meet your specific needs.
By offering the complete range of friction welding options, MTI can help you achieve the highest quality, efficiency, and performance in your welded assemblies. Trust us to guide you in selecting the optimal welding process for your application, backed by our unparalleled experience and innovation in the field.
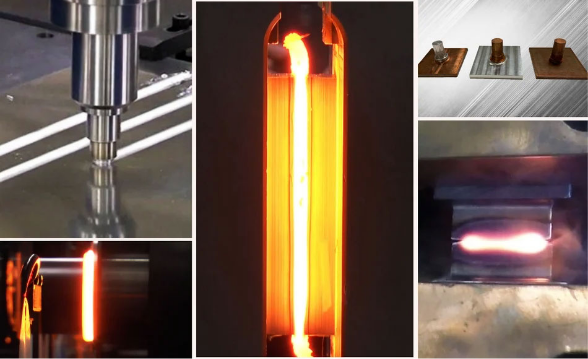
Low Force Friction Welding
MTI’s newest friction welding technology
Low Force friction welding uses external heat to reduce the forces of traditional welding methods to create a solid-state weld.
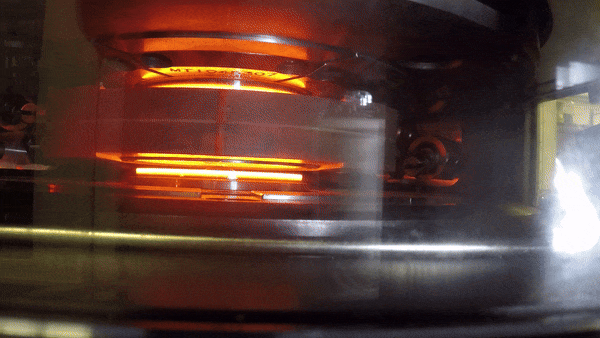
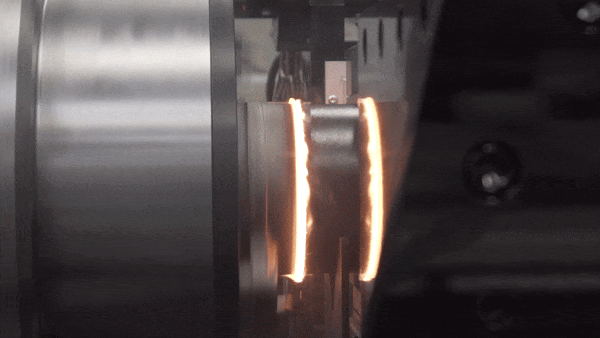
Rotary Friction Welding
Efficient, high-strength joining with direct drive, inertia or hybrid.
Rotary Friction welding is a solid-state process where one component is rotated at high speed and pressed against a stationary part. The resulting friction generates heat, forging the parts together seamlessly.
Linear Friction Welding
Widely used in the Aerospace industry and ideal for complex components
Linear friction welding joins two components by holding one part stationary while the other is pressed against it and moved in a high-speed linear motion.
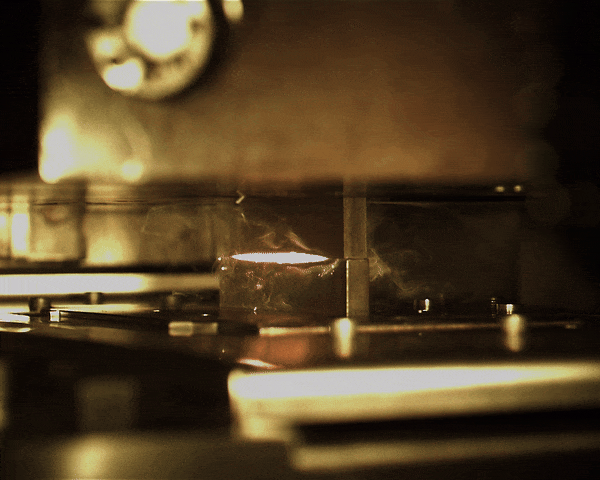

Friction Stir Welding
Transforming industries across the globe
Friction Stir Welding creates friction with a rotating pin tool that stirs across the materials in a weld line, effective for virtually defect-free bonding in aerospace, automotive, and other industries.
Check Your Material Combination & Geometry
Can Your Application Be Friction Welded?
Compatible Welds
|
Not Seeing Your Combination Of Materials?
That doesn’t mean it can’t be done. Many of our material combinations are also proprietary. That’s why several of our customers use MTI’s in-house metallurgy lab, which will test your materials for strength and durability to see if friction welding is the right process for you.
Please note Weld strength is dependent on materials & geometry.
Joint Geometries
Friction Welding can join a wide range of part geometries
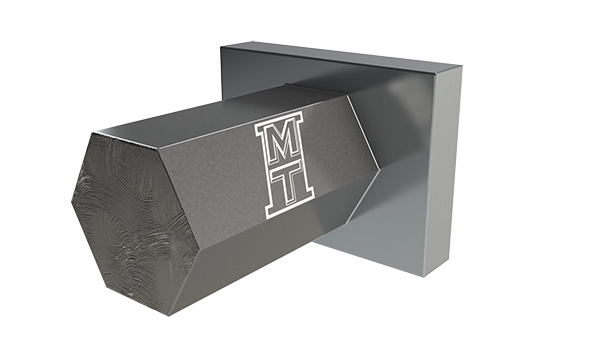
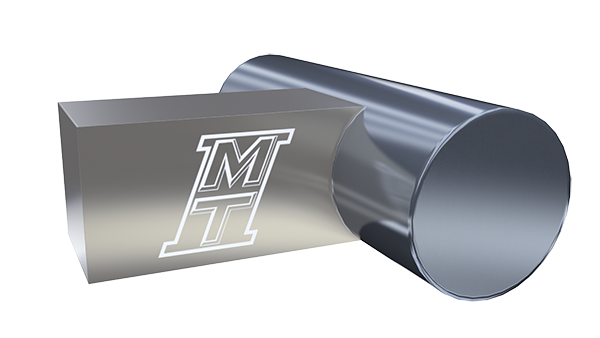
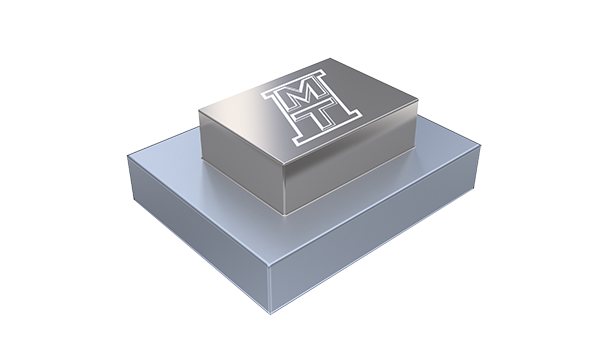
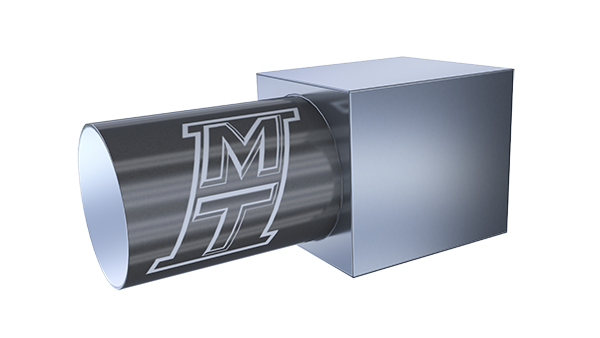
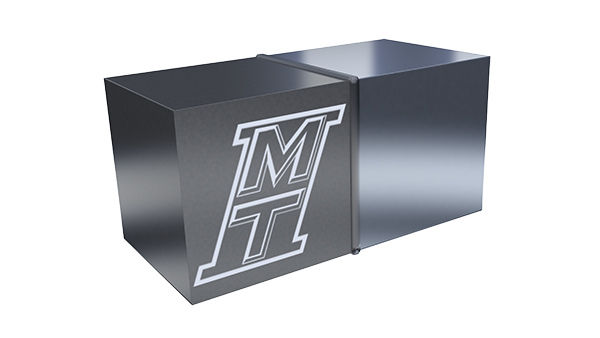
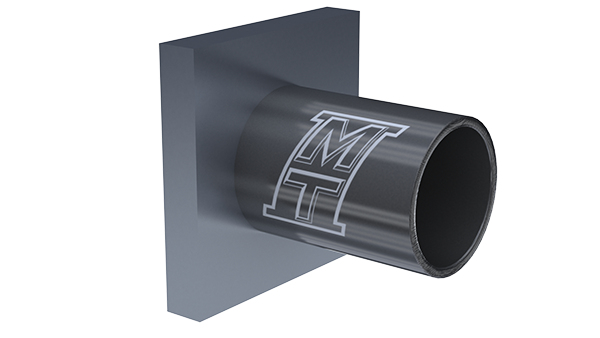
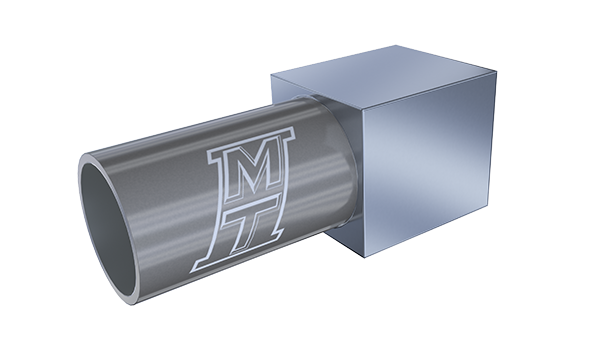
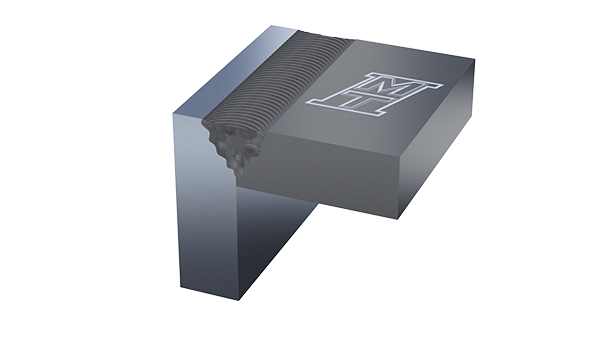
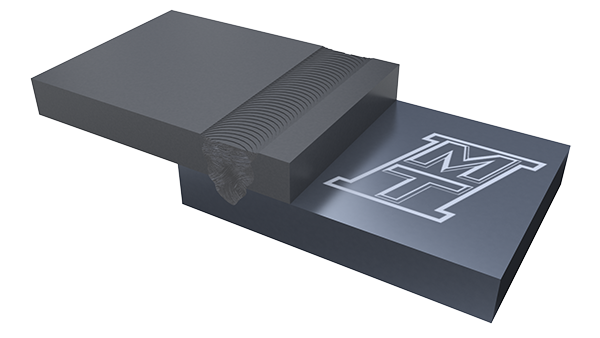
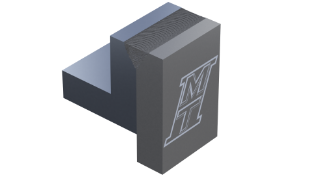
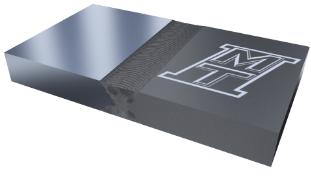
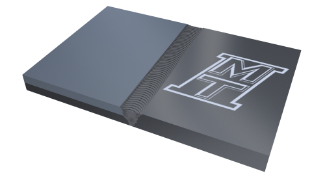
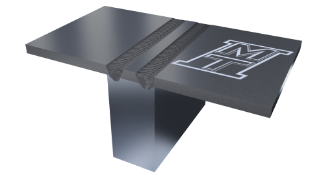
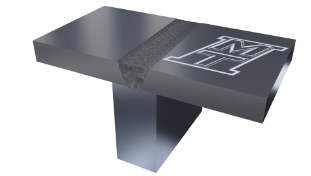
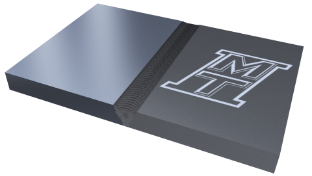
Let’s talk about the specifics of your project:
Example Parts
Friction Welding can join a wide range of parts and geometries
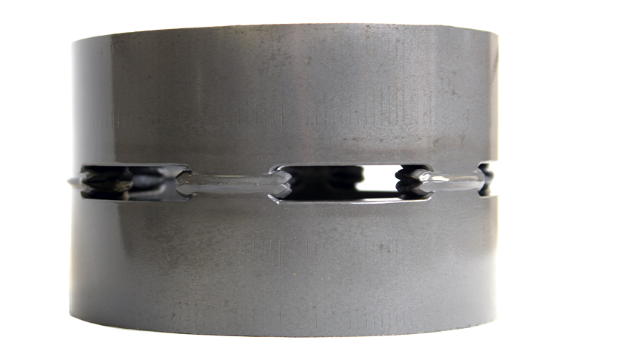
Application
Castellated Tube
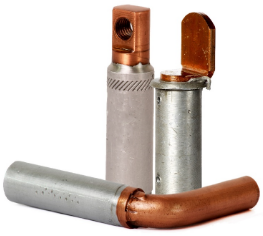
Application
Bimetallic electrical connectors
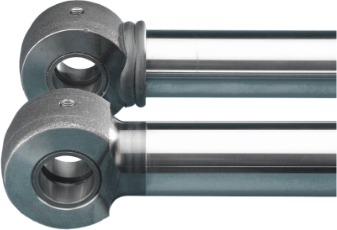
Application
Hydraulic Cylinder Rod
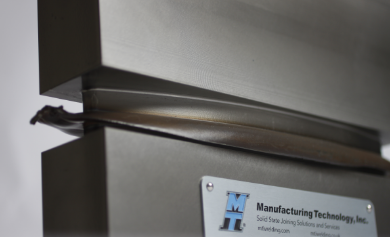
Application
Linear Aerospace Development
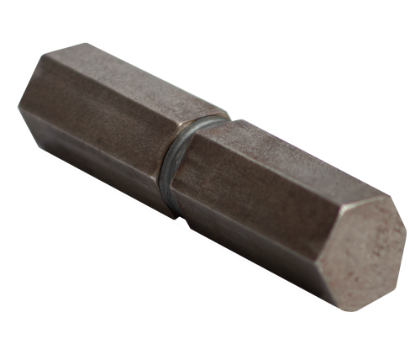
Application
Weld Orientation Development
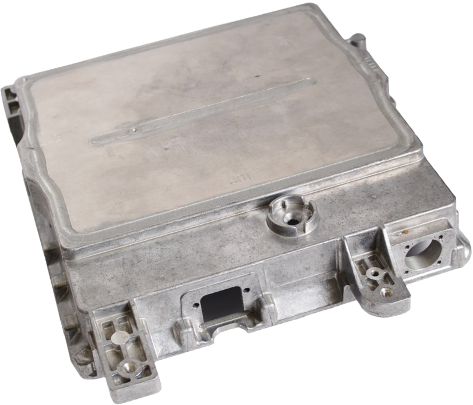
Application
Electronic Enclosure
Contract Friction Welding
We don’t just build friction welders – we operate them, too. When you partner with our global Contract Friction Welding teams, we will handle your project from start to finish on our state-of-the-art friction welding machines. Whether you need one part every year or one part every minute, we are here to help you reach your production goals across the globe.
Contract Friction Welding
We don’t just build friction welders – we operate them, too. When you partner with our global Contract Friction Welding teams, we will handle your project from start to finish on our state-of-the-art friction welding machines. Whether you need one part every year or one part every minute, we are here to help you reach your production goals across the globe.
Friction Welding Machines
MTI is the world-leader in designing and building Friction Welding machines. With 800+ machines shipped to over 35 countries, we are your trusted supplier.
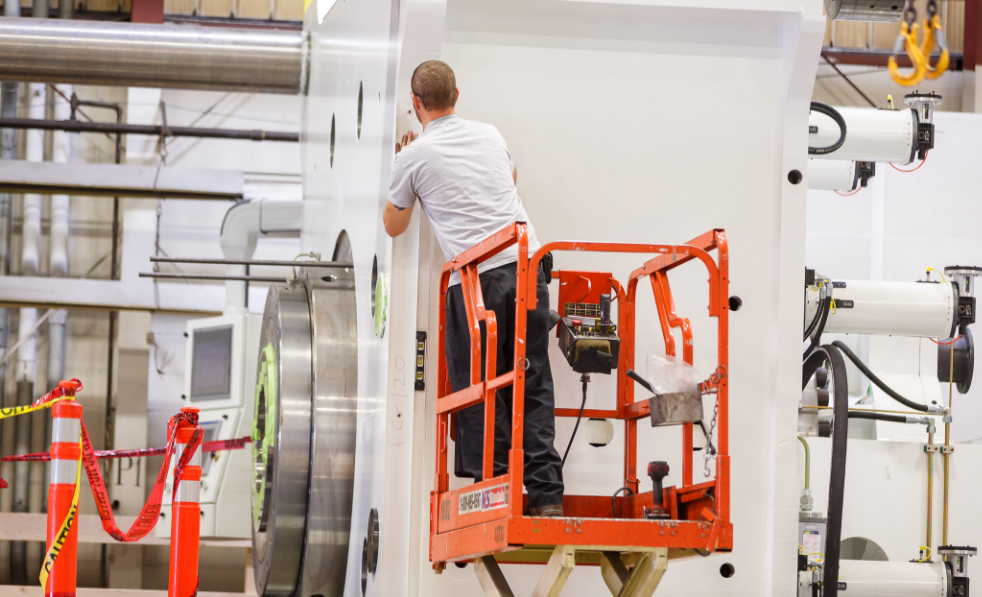
Learning Center
Case Studies
Videos
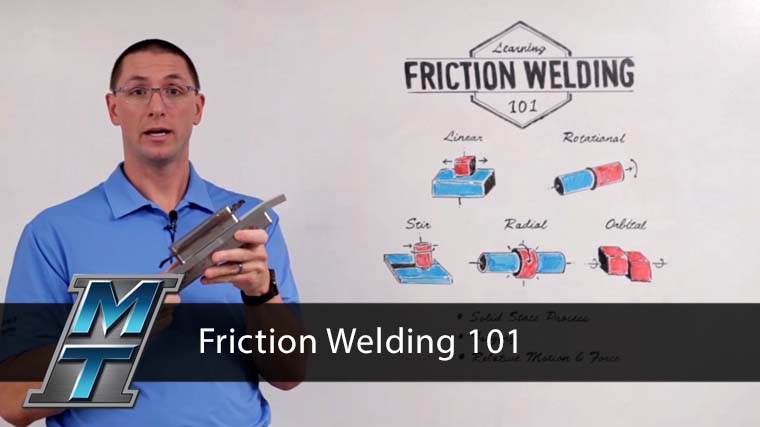
Whiteboard Wednesday
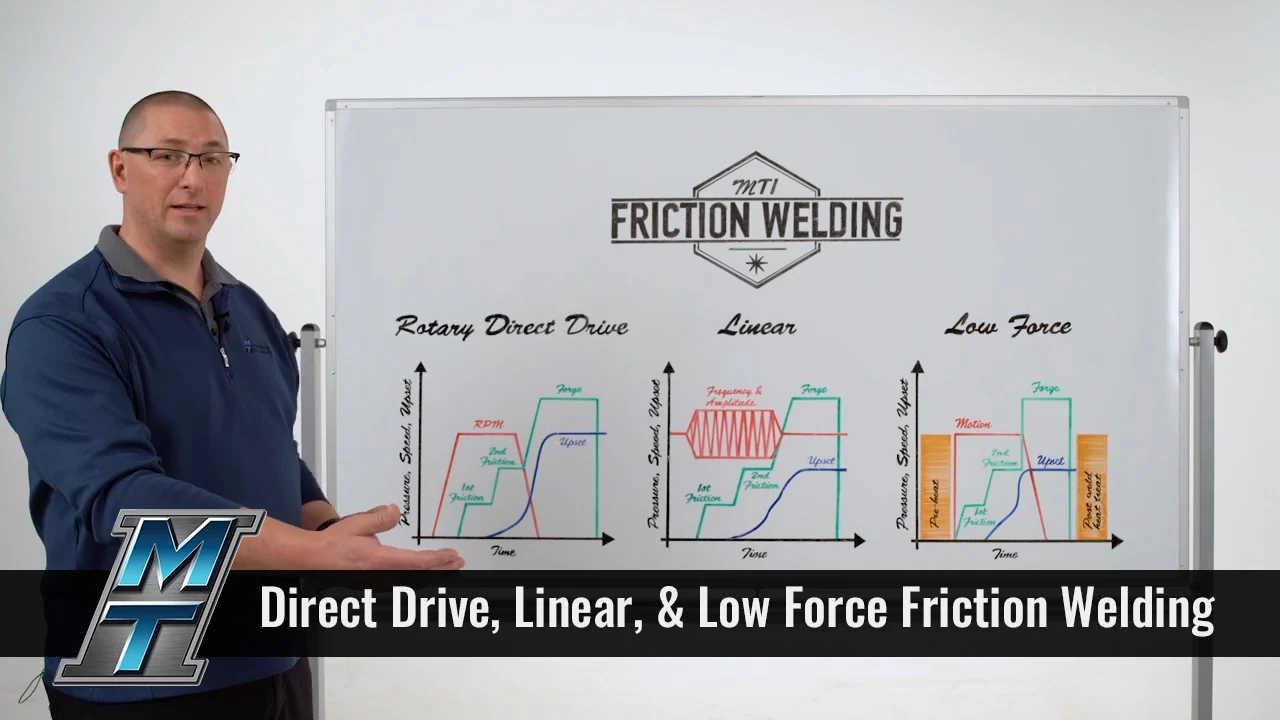
Whiteboard Wednesday
Get the information you need, before you need it — free and straight to your inbox from industry experts.
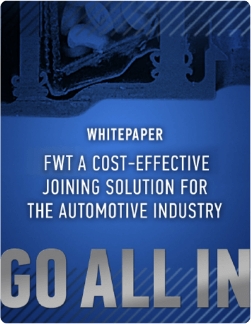
MTI White Papers
FWT: A cost-effective joining solution for the automotive industry
In the following pages, we will outline the benefits of friction welding, define the different types of friction welding, and describe the friction welding process. We’ll also mention current issues faced by the automotive industry. And finally, we’ll show how FWT is an effective tool to overcome these challenges and achieve manufacturing goals.